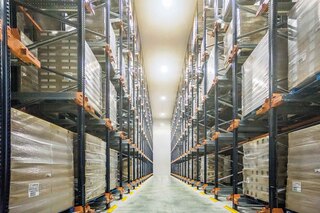
Stock minimo: strategie per una gestione efficiente
All’interno di un inventario sono presenti diverse tipologie di scorte a cui corrispondono diverse funzioni. I prodotti immagazzinati diminuiscono in quantità man mano che vengono emessi gli ordini e, in risposta a queste fluttuazioni, troviamo due concetti chiave:
- La scorta massima determinata dalla capacità di stoccaggio del magazzino e dalle politiche di approvvigionamento.
- La scorta minima indica il punto in cui è necessario procedere a un nuovo ordine (indicando il reorder point). Ne abbiamo parlato dettagliatamente nell’articolo dedicato alla scorta di sicurezza.
Entrambi i concetti sono compresi nel modello di rifornimento minimo/massimo, ovvero il metodo di controllo dello stock più consolidato tra le imprese. Nel nostro articolo ne analizziamo pro e contro.
Il modello a minimo-massimo
Con il metodo minimo-massimo si fissa un punto di approvvigionamento che, seguendo il consumarsi delle merci a magazzino, permette di realizzare gli ordini al fine di mantenere i giusti livelli di stock.
La rappresentazione grafica di questo modello è a forma di sega e mostra due tipi di picchi: i picchi ascendenti che indicano l’acquisto di stock, e quelli discendenti che evidenziano la spedizione delle merci.
Si tratta di un metodo semplice da implementare, la cui esecuzione può essere automatizzata con sistemi ERP e WMS. In questo modo quando uno SKU o referenza raggiunge i livelli di stock minimo, il sistema invia una notifica o un ordine di approvvigionamento automatico.
Esistono diversi metodi per stabilire il livello minimo di stock e qui di seguito indichiamo le principali variabili per il calcolo di questo parametro:
- La previsione della domanda.
- Il lead time, ovvero il tempo di consegna impiegato dal fornitore.
- Il costo (volume) dell’ordine.
Rappresentazione grafica dei livelli di stock
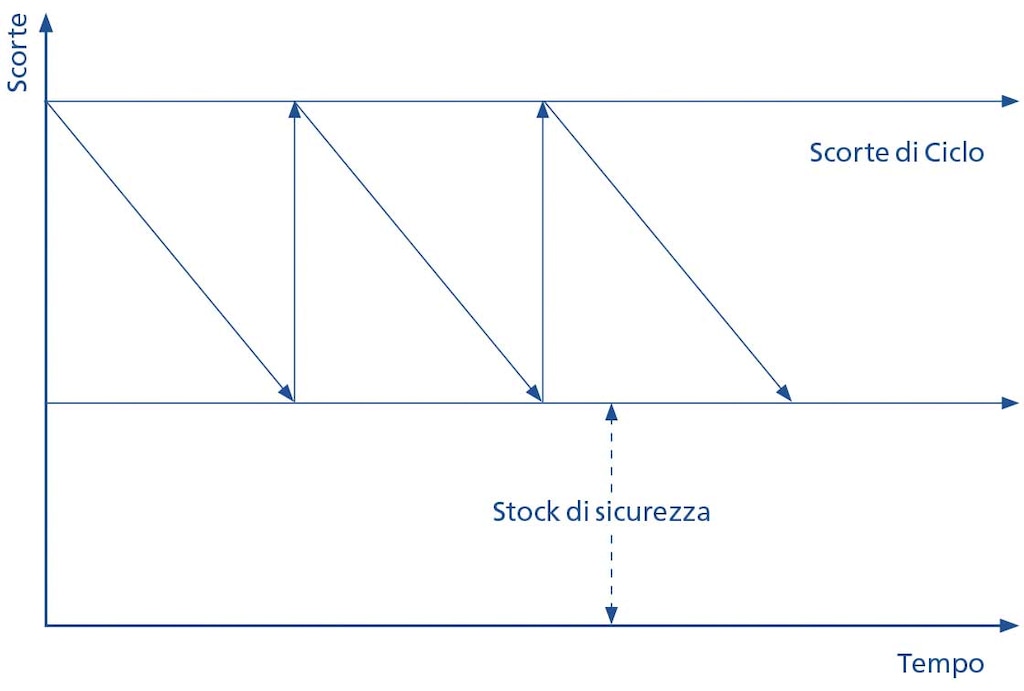
Limiti del modello a minimo-massimo
Il metodo dello stock minimo-massimo presenta alcuni difetti che è meglio approfondire.
- Tale modello parte da una prospettiva focalizzata su ogni SKU, senza considerare lo stato generale dell’inventario o dei fornitori. Ad esempio, potrebbe esserci un fornitore che ha una politica che prevede una spesa minima distribuibile tra tutti i prodotti del proprio catalogo. Con l’approccio di stock minimo-massimo, l'ordine verrebbe emesso solo una volta raggiunta la “spesa minima” indicata dal fornitore, aspetto che non è vantaggioso dal punto di vista economico.
- Non tiene sempre conto dell'evoluzione dei prodotti. Ogni codice attraversa un ciclo di vita con diverse fasi che influenzano la domanda (introduzione, crescita, maturità e declino). A meno che la regola dello stock minimo-massimo sia in continua revisione manuale (qualcosa che significherebbe perdere i vantaggi di automatizzare quel processo), applicare continuamente il rifornimento potrebbe significare accumulare scorte eccessive costose.
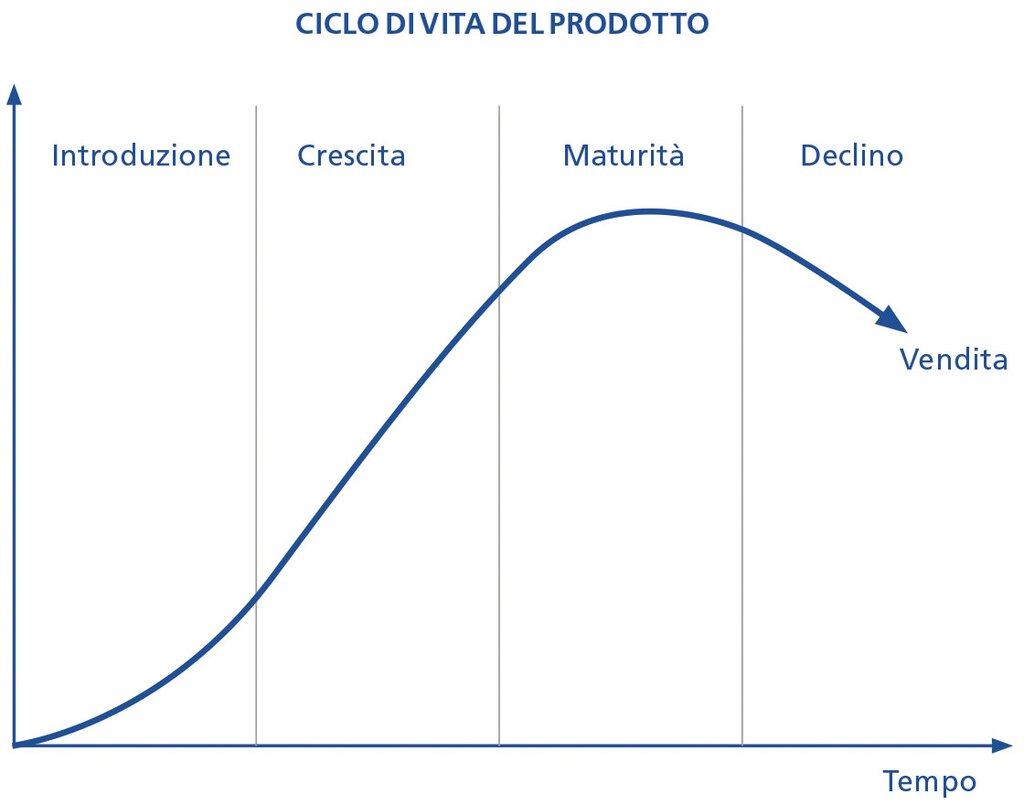
Vantaggi della gestione a stock minimo
Una delle conseguenze dell'applicazione di una rigida politica di scorta minima-massima è quella di accumulare più materiali del necessario. In effetti, l'ottimizzazione dello stock immagazzinato è uno dei pilastri della metodologia Lean logistics, poiché i vantaggi ad esso correlati sono noti:
- Diminuisce il capitale fermo in magazzino liberando risorse economiche che possono essere investite in altri aspetti, aumentando la liquidità dell’impresa.
- Si riducono i costi di stoccaggio legati alla conservazione dello stock. In più si contengono i rischi di obsolescenza legate alle risorse presenti in magazzino.
- È possibile liberare spazio in magazzino in modo da ampliare il proprio catalogo, potenziare l’area di picking o investire nell’acquisto dei materiali realmente necessari.
Come ottimizzare l’inventario per mantenere uno stock minimo
Abbiamo raccolto una serie di consigli e pratiche utili per poter lavorare sull’efficienza di questo tipo di scorta, li elenchiamo qui di seguito:
- Classificare per priorità
Revisionando e classificando le scorte immagazzinate in base alla loro rotazione è possibile portare alla luce i materiali “dimenticati” che possono rendere inefficiente la gestione delle scorte.
In questo senso, il software per la gestione del magazzino consente non solo di eseguire conteggi ciclici e accurati dell’inventario, ma anche di disporre sempre di uno storico prezioso che faciliterà notevolmente l'attività di ottimizzazione delle scorte.
Inoltre, la gestione di queste informazioni sarà di grande aiuto per dare la priorità alle scorte minime ai codici più importanti in base a diversi parametri logistici: fatturato, margini di redditività, costi di approvvigionamento, ad esempio. In questo modo, la scorta minima di ogni referenza viene calcolato da un punto di vista globale e non individuale: i singoli materiali vengono acquistati in base ad un unico budget (condividono lo stesso investimento).
- Non solo numeri: pianifica considerando tutti i fattori logistici
In alcuni casi, il modello a minimo-massimo funziona in maniera invisibile, specie se è stato automatizzato. Tuttavia, è consigliabile pianificare il rifornimento tenendo conto di tutti i fattori che influenzano le operazioni logistiche, e non solo la quantità numerica di scorte.
In caso contrario, il magazzino potrebbe essere sovraccarico al ricevimento della merce o, se un ordine effettuato al fornitore viene configurato come spedizione automatica, la società perderebbe i vantaggi derivanti dal groupage o consolidamento dei carichi.
In ogni caso, il magazzino deve essere preparato per affrontare imprevisti di questo tipo. Avere un WMS consente al centro di eseguire ricevimenti non pianificati gestendo anche la disposizione delle merci sulle scaffalature.
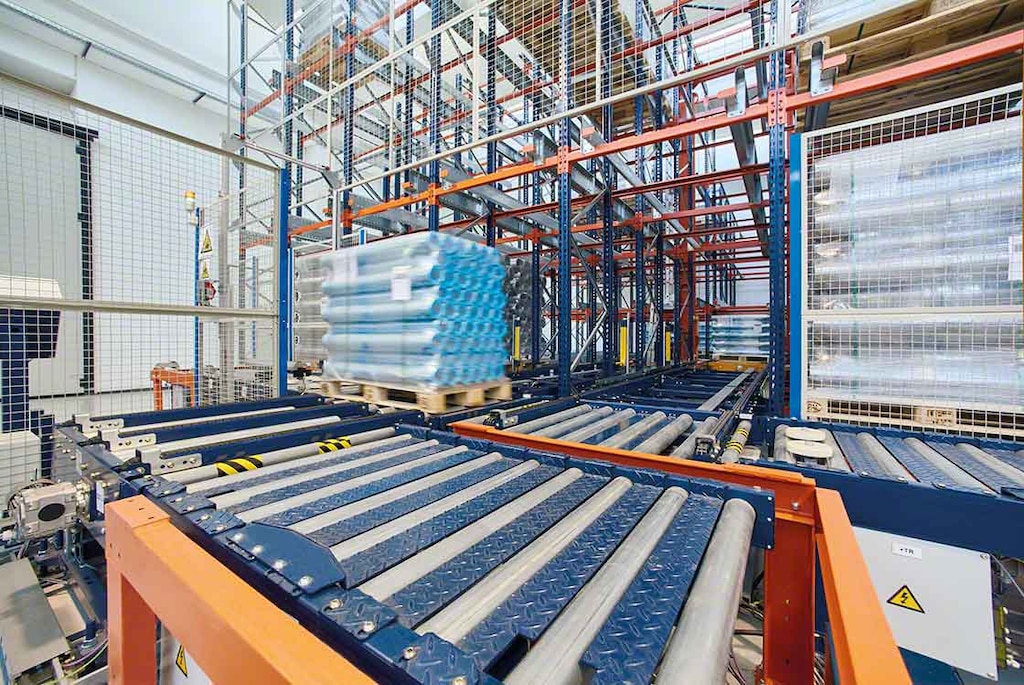
- Punta su un magazzino più efficiente e con meno costi operativi
La funzione principale delle scorte è di fornire all'azienda la capacità di rispondere alla domanda al momento giusto, nella forma e nei modi appropriati. Sebbene esistano strategie studiate per ottimizzare la quantità di stock a magazzino - vedi ad esempio il just in time - lo stoccaggio della merce resta necessario per il funzionamento della catena di approvvigionamento (la famosa Supply Chain).
Dato che lo stock minimo è indispensabile, bisogna ridurre i costi operativi abbattendo i tempi in cui le merci restano ferme in magazzino. Un approccio valido consiste nel lavorare per l'efficienza del magazzino, migliorandone i tempi di fornitura o i tempi di consegna (lead time). Questi possono essere suddivisi in:
- Lead time del trasporto reale delle merci da un luogo all’altro. Indubbiamente, l'automazione dei processi di magazzino come la movimentazione dei carichi, ad esempio, libera gli operatori che possono dedicarsi a compiti più complessi e meno ripetitivi.
- Lead time delle informazioni, ovvero il tempo necessario a processare gli ordini, a creare le liste di picking e stabilire una gerarchia di priorità. I WMS sono lo strumento ideale per ridurre i tempi di ciclo e per efficientare le operative del magazzino.
Va sottolineata l’importanza del controllo dei livelli di scorte in quanto serve a prevenire la temuta rottura di stock e il sovradimensionamento delle scorte di sicurezza. I software moderni di Mecalux presentano moduli in grado di monitorare la performance attraverso i principali KPI di magazzino.
Stock minimo: una sfida complessa ma non impossibile
L'impatto finanziario dell'accumulo di scorte e la crescente variabilità della domanda hanno costretto numerose aziende a cambiare la propria politica di gestione delle scorte. Ciò ha rivelato i limiti del modello a minimo-massimo. Cercare di adattarlo a una realtà sempre più complessa implica integrare software avanzati nella gestione della logistica, oltre a basare le decisioni strategiche su dati misurabili.
Se stai cercando di trasformare il magazzino in un'installazione efficiente, contattaci e ti mostreremo le nostre soluzioni di stoccaggio tradizionali, automatiche e digitali.