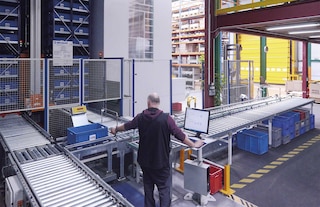
Ciclo di Deming (PDCA) nella logistica
Il ciclo Deming o ciclo PDCA (Plan, Do, Check e Act), è un metodo di gestione della qualità che consente di attuare una strategia di miglioramento continuo in azienda, facilitando così la risoluzione dei problemi in modo strutturato e sistematico. Questa procedura è composta da quattro fasi fondamentali: pianificazione, esecuzione, controllo e adeguamento.
Il nome della procedura proviene dal cognome di William Edwards Deming, sebbene la creazione della stessa sia attribuita al suo mentore, Walter Shewhart. Deming, esperto di sistemi di gestione della qualità e di statistica, lavorò con ingegneri e scienziati per applicare il ciclo PDCA alle aziende giapponesi negli anni '50. Solo tre decenni dopo la sua metodologia sarebbe stata applicata anche all’interno delle aziende americane.
Cos’è il ciclo PDCA?
Il ciclo PDCA, chiamato anche spirale di miglioramento continuo, è una metodologia volta a migliorare una procedura attraverso prima l’individuazione della causa di un problema, che verrà in seguito corretta. Il ciclo di Deming viene normalmente mostrato come una ruota, in quanto concepito come un processo circolare. Lo rappresentiamo di seguito:
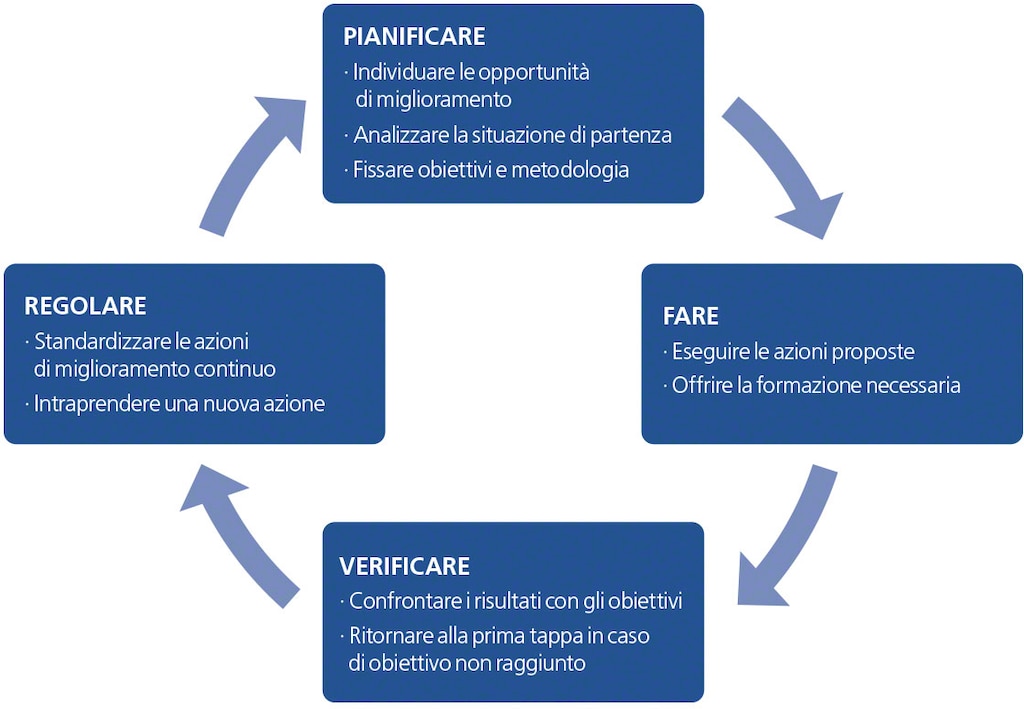
Il ciclo PDCA prevede la pianificazione di un'azione di miglioramento individuata a partire da un problema ricorrente; l'esecuzione della soluzione proposta; la successiva analisi dell'operazione realizzata al fine di identificare le differenze tra ciò che è pianificato e ciò che viene eseguito; infine, la standardizzazione necessaria per implementare il nuovo processo in azienda.
Le quattro fasi della ruota di Deming
Vediamo nel dettaglio cosa comprende ciascuna delle fasi del ciclo PDCA:
1. Pianificare
L'obiettivo di questa fase è definire il problema o la procedura che si desidera migliorare. Nella logistica esistono delle operazioni e dei processi che possono essere sottoposti al ciclo Deming: errori nelle fasi di pick & pack, ritardi nella preparazione degli ordini, la gestione di un alto tasso di resi o la consegna di pacchi danneggiati. In questo senso è essenziale il controllo del magazzino basato sugli indicatori di prestazione.
La fase di pianificazione del ciclo di Deming può essere suddivisa in tre sottoprocessi che servono a portare a termine tre azioni:
1. Determinare le opportunità di miglioramento e analizzare la situazione di partenza. In questa azione è necessario porre l'accento sulle cause che stanno generando il problema. Il Principio di Pareto può esserci utile. Proprio come avviene con l’analisi ABC del magazzino, questo principio può essere utilizzato per stabilire le priorità: la maggior parte degli effetti negativi di un problema (80%) sono causati da alcune cause (20%).
2. Stabilire obiettivi misurabili. Questi devono essere specifici, realizzabili, pertinenti e orientati ai risultati. Gli obiettivi possono essere generati in base allo storico dei KPI o in dati settoriali derivanti dal processo di benchmarking.
3. Preparare il piano d'azione. Questo sottoprocesso include lo studio e la selezione delle opzioni correttive più appropriate, dei responsabili di ciascuna azione e delle date di esecuzione. Può essere pensato come un test pilota che verrà successivamente esteso ad altre aree se i risultati risultassero soddisfacenti.
2. Fare
La fase "Do" può essere considerata come la fase di test. Consiste nell'eseguire l'azione scelta e ad eliminare le cause del problema. Affinché si svolga senza intoppi, è buona prassi preparare istruzioni e formare i dipendenti coinvolti, oltre a registrare eventuali deviazioni dal piano iniziale.
3. Verificare
L'obiettivo è valutare i risultati mettendo a confronto il piano eseguito e quello pianificato sulla base delle informazioni raccolte (generalmente visualizzate attraverso grafici e diagrammi). In questa fase è cruciale il rispetto delle scadenze stabilite, in modo da evitare conclusioni affrettate.
Una volta valutati i risultati, possono presentarsi due scenari
- L'obiettivo è stato raggiunto e il ciclo Deming passa alla fase successiva di regolazione. È essenziale controllare le altre metriche in modo che non vi siano "effetti collaterali", ovvero che non si sia generato o in altre aree a seguito del ciclo.
- L'obiettivo non è stato raggiunto. In questo caso può essere necessario analizzare la fase precedente e, qualora non fosse sufficiente, tornare all'inizio del ciclo di Deming e analizzare nuovamente le cause che hanno dato origine al problema.
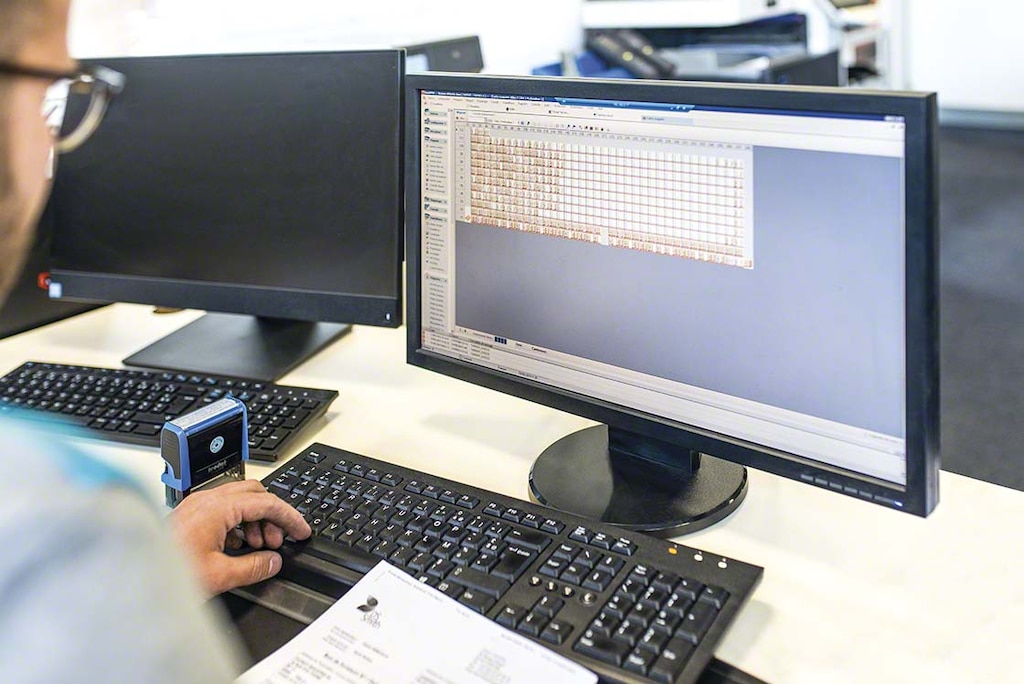
4. Agire
Se il ciclo si è dimostrato efficace, la modifica va documentata, standardizzata e controllata. Si consiglia di rendere disponibili queste informazioni al personale organizzando, ad esempio, sessioni di formazione. Per un monitoraggio esaustivo dei nuovi processi, è importante definire gli indicatori chiave di prestazione da analizzare.
Se sono stati testati con successo nuovi strumenti, andrebbero applicati in maniera più estesa. Ad esempio: se l’uso di dispositivi di picking vocale è servito a ridurre gli errori di picking, è auspicabile estenderne l’utilizzo a tutti gli operatori.
Vantaggi del ciclo di Deming
Elenchiamo ora i principali vantaggi dell'applicazione del ciclo Deming:
- Fornisce un metodo standardizzato che può essere utilizzato in qualsiasi area di business per risolvere problemi ricorrenti.
- Si risparmia tempo nella ricerca della soluzione più efficace.
- Funziona come una tabella di marcia capace di garantire la completa esecuzione di un progetto.
- Garantisce un'analisi dettagliata degli errori comuni, utile per la loro risoluzione.
- Viene utilizzato per controllare e documentare l'avvio di nuovi processi.
- Il ciclo PDCA stabilisce le linee guida per eliminare le cause di un problema, indipendentemente dai cambi di personale.
- Favorisce il lavoro di squadra grazie alla partecipazione attiva di tutti i soggetti coinvolti.
In che modo il ciclo PDCA migliora la qualità logistica di un'azienda?
Nella logistica per qualità si intende la capacità di soddisfare la domanda dei clienti, al minor costo e senza compromettere il livello di servizio. La chiave è trovare l'equilibrio ottimale tra costi e qualità del servizio.
I costi della qualità e della non qualità
A tal proposito esistono due tipi di costi:
- Costi di qualità: sono quelli che permettono di ottenere la qualità richiesta, per esempio il costo legato alla manutenzione preventiva dei sistemi di magazzino.
- Costi di non qualità: sono tutte le spese che un’azienda affronta a causa della mancanza di qualità nei processi. Non bisogna sottovalutarli perché potrebbero generare delle perdite economiche, basti pensare ai costi derivanti da un fermo macchina o da un’avaria, ad esempio.
Strumenti per la gestione efficiente del magazzino
Il miglioramento della qualità è un obiettivo costante nella logistica, poiché è sinonimo di maggiore produttività. Per questo, applicare metodi come il ciclo di Deming ai processi di magazzino è la chiave di volta per aumentare l'efficienza logistica dell'azienda.
Il PDCA può essere supportato da sistemi e attrezzature che ottimizzano i processi presenti in uno spazio logistico. L’implementazione di un software WMS favorisce l'applicazione di questo metodo, poiché raccoglie ed elabora automaticamente un enorme volume di informazioni.
Se poi si scelgono moduli specifici, per esempio Supply Chain Business Intelligence, si otterrà una gestione automatica dei flussi logistici sempre accompagnata da dati strutturati e grafici personalizzati facili da interpretare.
Strumenti per la gestione efficiente del magazzino
L'obiettivo finale della qualità logistica è ottenere un miglioramento continuo del servizio, riducendo al massimo i costi. I dati contenuti nel Supply Chain Digital and Analytics Survey di Deloitte parlano chiaro: per due intervistati su dieci la riduzione dei costi logistici è alla base degli investimenti in strumenti di analisi dei dati.
Dopotutto lo diceva anche Deming che senza dati siamo solo persone con un’opinione. Pertanto il ciclo PDCA può essere applicato in modo efficace solo ricorrendo a sistemi informatici in grado di strutturare i dati in KPI facilmente interpretabili. Per saperne di più sui vantaggi legati all’utilizzo di un software per la gestione del magazzino, contattaci e ti forniremo tutte le informazioni di cui hai bisogno.