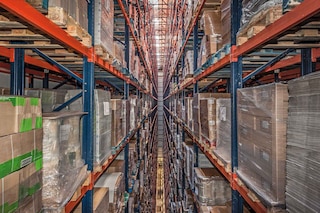
L’importanza del punto di riordino nella gestione delle scorte
Con l’espressione punto di riordino o reorder point (ROP) ci si riferisce al momento in cui si raggiunge un livello di scorte tale da rendere necessaria l’emissione di un ordine al fornitore. In tal maniera si effettua il riapprovvigionamento, ovvero l’acquisto delle materie prime e delle risorse necessarie ad evitare una rottura di stock.
Quando si pianifica la fase di approvvigionamento delle scorte di magazzino, è necessario rispondere a due domande fondamentali: quando effettuare un nuovo ordine, e in che quantità ordinare?
Le risposte dipendono dal tipo di gestione dello stock applicato nel magazzino e dal livello delle scorte di sicurezza stabilito, aspetto questo strettamente legato al punto di riordino.
Modello di gestione deterministico e probabilistico
Al momento di gestire lo stock di un'impresa, uno dei principali fattori che condizionano le strategie logistiche sono il tipo di domanda e la variabilità della stessa. A tal proposito si possono adottare due metodi di gestione dello scorte:
Metodo di gestione deterministico (basato sul modello di Wilson)
Questa metodologia si fonda su una domanda regolare (statica nel tempo), che si traduce in un tasso di consumo costante e quindi prevedibile (in realtà, però, sorgono sempre incongruenze che ne alterano la traiettoria, rendendola dinamica).
Il modello di Wilson rientrerebbe in questo metodo di gestione dell’inventario, ovvero su una gestione del livello di riordino che si articola intorno a una domanda annuale costante e su costi fissi (indipendentemente del volume).
La prospettiva deterministica è di stampo classico e i modelli basati su questo paradigma risultano sicuramente più facili da implementare, ma denotano una certa distanza dalla domanda reale.
Metodo di gestione probabilistico (o stocastico)
In questo modello non esiste un valore esatto o costante che definisca in maniera statica la domanda, però è possibile realizzare calcoli e previsioni a partire da modelli probabilistici che variano nel tempo. Tali pronostici si ottengono grazie a calcoli più complessi, per i quali si utilizza un software dedicato di demand forecasting.
La scelta di un metodo o di un altro andrà a incidere direttamente sul calcolo del punto di riordino.
Calcolo del punto di riordino per approvvigionamento
Il reorder point serve a raggiungere un equilibrio tra i costi delle scorte e il rischio di rimanerne senza (out-of-stock). Fatta questa premessa, si può stabilire un punto di riordino periodico (ad esempio un determinato giorno della settimana) o soggetto a revisione continua.
Generalmente i responsabili della logistica optano per la seconda opzione, poiché è più flessibile e contempla sia l'eterogeneità dei prodotti immagazzinati sia la variabilità della domanda nel tempo.
Per calcolare il punto di riordino, è opportuno considerare i seguenti fattori:
- I livelli di stock di sicurezza necessari per scongiurare un esaurimento delle scorte. Questo aspetto è vincolato al livello di servizio.
- Il lead time o tempo di consegna dei fornitori. Questo è il tempo necessario affinché un fornitore gestisca l'ordine e invii la merce. Può anche riferirsi al tempo necessario per produrre la merce. Se gli ordini di acquisto vengono inviati a fornitori diversi, è auspicabile considerare l’insieme dei tempi di consegna e stabilire diversi reorder point.
- Possibili consumi e picchi di domanda inaspettati di un prodotto e in un certo intervallo di tempo (di solito giorni).
Una volta considerati questi aspetti, passiamo ad analizzare la formula del punto di riordino, che sarebbe la seguente:
Punto di riordino = scorta di sicurezza + (consumo medio x lead time o tempo di consegna del fornitore)
Facciamo un esempio pratico per rendere il tutto più chiaro. Supponiamo che un’impresa gestisca una domanda giornaliera (dal lunedì al venerdì) di 500 unità, che il lead time del fornitore sia di 5 giorni e che lo stock di sicurezza per questa referenza sia pari a 100 unità. La formula in questo caso sarebbe la seguente:
Punto di riordino = 100 + (500 x 5) = 2.600 unità
Pertanto l’impresa deve procedere al riapprovvigionamento quando le giacenze presenti in magazzino sono pari a 2.600, coprendo la domanda con le proprie scorte durante il tempo che il fornitore impiega a inviare i suoi prodotti.
Diagramma a “denti di sega” del reorder point
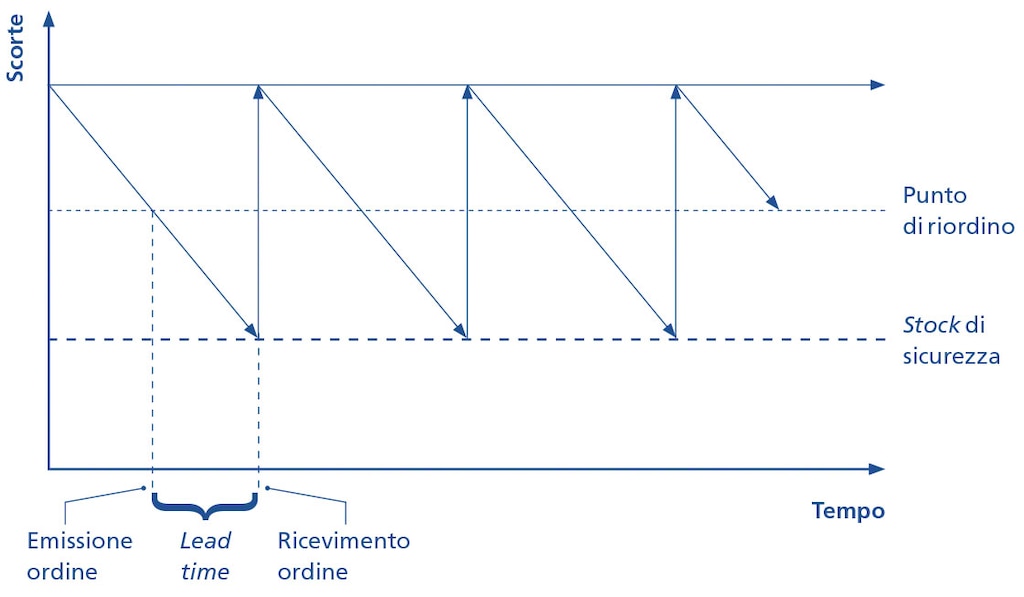
Il reorder point visto dal magazzino: come renderlo più preciso
Quando si raggiunge il livello di riordino si attiva la fase di rifornimento. Durante essa è essenziale una gestione fluida delle scorte a magazzino, degli ordini e delle successive fasi di ricevimento merci. L'obiettivo è evitare squilibri che potrebbero compromettere da un lato la capacità di stoccaggio del magazzino, dall’altro gli investimenti finanziari destinati alle scorte.
Ma in che modo il magazzino può agevolare la gestione delle scorte e il calcolo del punto d'ordine? Ecco alcune strategie per ottimizzare i processi di approvvigionamento.
Precisione dei dati relativi allo stock a magazzino
Ogni magazzino possiede un registro informatizzato delle scorte con i dati relativi alle merci disponibili in stock. L'ERP è di solito il contenitore di queste informazioni, dato che è il sistema che collega a livello informatico tutte le aree logistiche dell'azienda.
Il magazzino deve fornire dati costantemente aggiornati e accurati, onde evitare che il livello di reorder point venga calcolato sulla base di informazioni errate, che potrebbero causare gravi incongruenze di inventario.
Per ridurre le possibilità di errore, si consiglia l’utilizzo di un software per la gestione del magazzino (WMS) in grado di monitorare i movimenti delle merci all’interno dello spazio logistico e di raccogliere dati in tempo reale. Ciò permette di avere una fotografia esatta delle scorte disponibili e di pianificare meglio gli ordini.
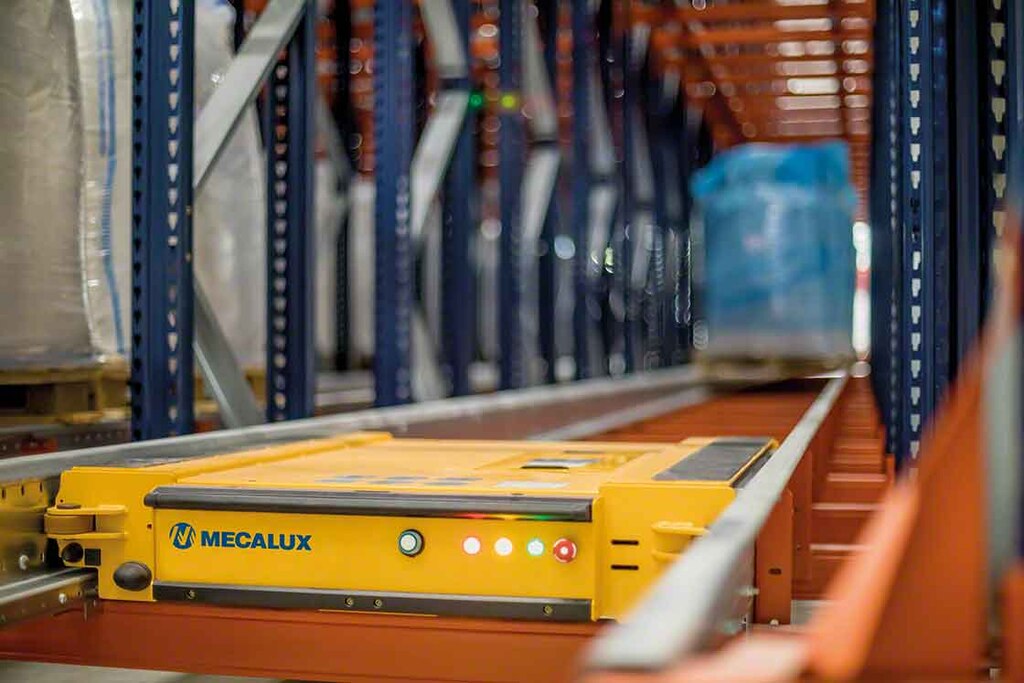
Controllo dei lead time dei fornitori e del magazzino
Quando il livello delle scorte raggiunge il punto di riordino, si emette un ordine che viene concepito come unico per ogni codice SKU. Nonostante ciò, la gestione dello stock può complicarsi quando si lavora con più fornitori che forniscono all’impresa la stessa referenza, rendendo più complesso il controllo dell’indice di rotazione relativo a ogni codice.
In casi come questi vale la pena lavorare sul calcolo del livello di riordino impostandolo sulla domanda, fissando per lo meno due reorder point:
- Il primo reorder point è vincolato agli ordini da inviare al fornitore più conveniente a livello di costi, ma più lento in fase di consegna (la convenienza è la ragione che motiva la scelta di questo fornitore).
- Il secondo reorder point invece va legato al fornitore che offre lead time più corti. Questo punto di riordino può essere previsto per scongiurare un out-of-stock qualora il fornitore più lento dovesse ritardare una consegna.
Parallelamente, per fissare diversi reorder point, bisogna considerare anche i tempi operativi del magazzino per la gestione fisica delle merci (ricevimento, stoccaggio, riapprovvigionamento ecc.)
Considerati tutti questi fattori, e nei casi specifici in cui le scadenze sono “pericolosamente” ridotte, il software WMS sarà decisivo per evitare rotture di stock, per le seguenti ragioni:
- In quanto aiuta a stabilire un ordine di priorità in base a parametri logistici specifici (i percorsi di trasporto o i tempi di consegna, tra gli altri).
- Perché agevola l’organizzazione delle fasi di ricevimento merci, controllo qualità e rifornimento del magazzino.
- Poiché permette di applicare strategie di lean o di bypassare lo stoccaggio grazie tecniche come il cross docking.
Reattività e rapidità, fattori chiave per una gestione efficiente del magazzino
Stabilire un punto di riordino è fondamentale per evitare un out-of-stock. Quando si tratta di rifornire gli scaffali, è importante pianificare bene gli acquisti per evitare un sovradimensionamento dello stock (con relativi costi annessi). Al contempo, le imprese devono sviluppare una certa reattività, utile in caso di imprevisti.
La gestione efficiente delle scorte e del reorder point passa dunque per i sistemi di gestione del magazzino. Questi dovranno essere in grado di adattarsi a qualsiasi strategia operativa garantire i tempi di reazione veloci tanto necessari nella logistica moderna.
I software giocano un ruolo chiave. Grazie ai moduli dedicati all’analisi della catena logistica, i responsabili di magazzino possono visualizzare lo stato di ciascuna operazione, comprese le informazioni relative al livello di riordino, come ad esempio: il pannello del cliente (percentuale di referenze in magazzino, percentuale di ordini in sospeso, spedizioni puntuali, tempi di ciclo) o capacità del magazzino (densità di utilizzo delle posizioni, volume di occupazione per tipo di posizione, posizioni utilizzate per tipo di articolo ecc.)
La logistica moderna punta su sistemi di stoccaggio efficienti, sull’automazione e su programmi digitali in grado di far funzionare il magazzino come un orologio svizzero. Se vuoi migliorare il rendimento del tuo spazio logistico, contattaci.