Un flusso non sempre è lineare. In altre parole, non in tutti i magazzini le merci arrivano, si conservano e poi escono nuovamente seguendo tre semplici step. Al contrario, possono presentarsi situazioni ben più complesse. A tal proposito, un flusso di magazzino può essere semplice, medio o complesso. In questo articolo ne analizzeremo le caratteristiche con l'aiuto delle immagini che mostrano i diagrammi di flusso.
Il flusso dei materiali o delle merci può articolarsi in vari modi a seconda della complessità del prodotto da movimentare o del tipo di impianto in cui verrà stoccato. Esistono diverse tipologie, suddivise in funzione del grado di complessità che presentano:
- Flusso medio: è la tipologia di flusso presente nei magazzini che eseguono operazioni di picking semplici o combinate, generalmente, con la fornitura di pallet completi. In questo caso, dopo le fasi di ricevimento, le merci passano a un magazzino generale da cui vengono smistate verso la spedizione o direttamente verso l'area di consolidamento.
- Flusso complesso: si realizza negli impianti che dispongono solitamente di aree di movimentazione intermedie e possono richiedere più interventi operativi che prevedono flussi di una certa complessità. In questo diagramma si osserva un esempio di flusso in impianti complessi (include tutte le diramazioni possibili).
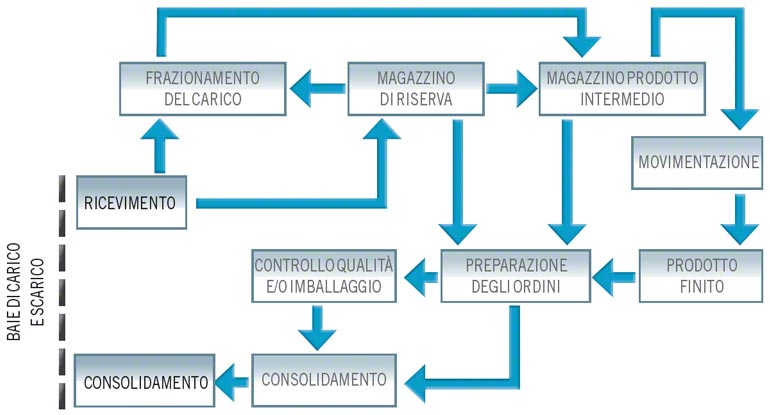
Diversi flussi, diversi costi
L'aggiunta di un flusso rappresenta un ulteriore costo che si somma all’importo complessivo del processo all'interno del magazzino. Quanto maggiore è il frazionamento da effettuare delle unità di carico, tanto più elevati saranno i costi. Le operazioni di picking sono quelle che incidono maggiormente - oltre il 60% - sull'importo complessivo degli interventi operativi nel magazzino, da cui deriva l’importanza di una corretta progettazione di queste aree. Per questo si ricorre a dispositivi che supportano le attività di selezione e prelievo, come ad esempio i sistemi pick-to-light.
D'altro canto, più grande è il magazzino, maggiori sono le distanze che devono coprire i mezzi di movimentazione e il personale, motivo per il quale il costo finale risulta maggiore. Nei centri con un elevato numero di movimentazioni vale la pena ricorrere all'automatizzazione delle attività di picking in modo tale che sia il prodotto a viaggiare verso l’uomo (goods-to-men).
Flussi e rotazione dei prodotti
Nella gestione dei flussi logistici, è importante distribuire le referenze sugli scaffali tenendo conto del loro indice di rotazione e dello spazio che occupano. Le merci di maggiori dimensioni e i prodotti ad alta rotazione dovrebbero essere conservati in prossimità delle baie di carico e scarico allo scopo di efficientare le attività di movimentazione.
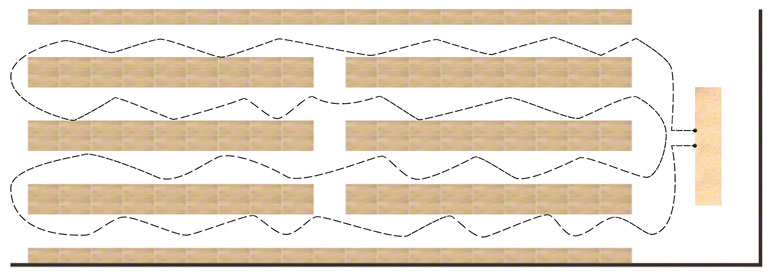
Installazione per picking "uomo alla merce"
Installazione per picking "merci all'uomo"
Inoltre, come abbiamo già illustrato nella sezione dedicata alle unità di carico, un solo pallet può contenere centinaia di unità di vendita. Conseguentemente, eseguendo una sola operazione di movimentazione, è possibile risparmiare i numerosi passaggi necessari per movimentare ciascun prodotto sfuso. Per massimizzare l'efficienza, è possibile far sì che lo stesso operatore svolga il maggior numero possibile di azioni in un periodo prestabilito. Questo principio può essere applicato a tutte la attività di magazzino.
La rotazione dei prodotti: A-B-C
Magazzino di prodotti di piccole dimensioni dedicato a ferramenta, forniture industriali, bricolage ed edilizia. Fonte: Mecalux.
Un altro dei fattori decisivi che condiziona l'andamento dei flussi logistici, è la domanda. In questo senso, gli articoli più richiesti devono essere alloggiati nei pressi delle baie di carico e scarico della merce. Per sapere quali articolo distribuire in tali aree, si ricorre allo studio degli indici di rotazione. Questi indicano il turnover delle scorte in magazzino e, al contempo, permettono di suddividere le merci in tre classi:
A. Alta rotazione: articoli molto richiesti che entrano ed escono continuamente.
B. Media rotazione: entrano ed escono abitualmente, ma in quantità minori rispetto alle merci di classe "A".
C. Bassa rotazione: sono le unità di carico che rimangono più tempo nel magazzino e che presentano una scarsa domanda.
I valori relativi all'indice di rotazione trovano poi uno strumento di doppia verifica nella teoria dell'80/20 o Diagramma di Pareto, secondo la quale l'80% delle vendite è concentrato sul 20% dei prodotti, mentre il restante 20% delle vendite si distribuisce tra l'80% dei prodotti rimanenti.
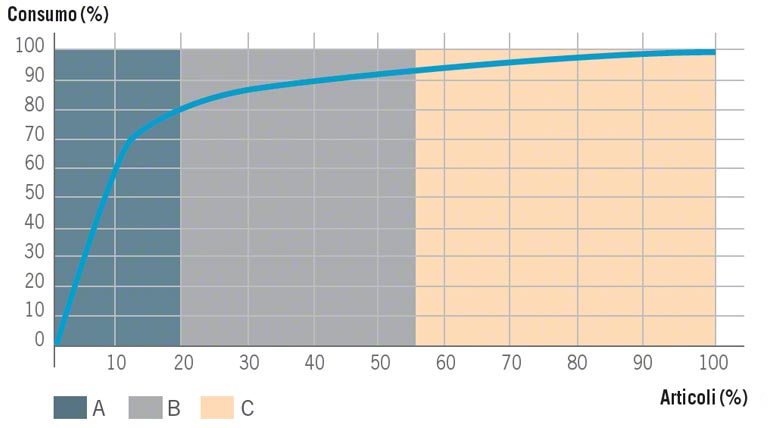
Rappresentazione grafica del Diagramma di Pareto.
Considerando entrambi questi fattori (rotazione e Pareto), il trattamento da riservare ai flussi deve essere diverso a seconda che si presenti una rotazione di tipo A, B o C. Nelle due immagini qui di seguito si illustrano due esempi di possibili criteri d'applicazione: la prima immagine mostra la disposizione delle merci sulle scaffalature all'interno del magazzino. Nella seconda immagine si mostra la distribuzione dei prodotti in verticale sugli scaffali.
Distribuzione dei prodotti all'interno del magazzino a seconda della rotazione.
Distribuzione su una scaffalatura (solitamente si applica al picking).
Nel primo esempio i prodotti di tipo A sono stati stoccati più vicino all'area di ricevimento e spedizione. Nel secondo esempio, i prodotti di tipo A sono stoccati nell'area più ergonomica della scaffalatura.
A volte è preferibile sistemare i prodotti raggruppati per sistema di stoccaggio, cercando di sfruttare al meglio lo spazio disponibile. In altre situazioni si premierà senza dubbio l'agilità e il risparmio di tempo per lo svolgimento delle operazioni. Nei casi in cui sia fattibile, si cercherà di combinare i due fattori.
Osservazioni finali sui flussi di magazzino
Per ottimizzare i flussi di magazzino e ridurre i costi legati alla movimentazione delle merci bastano pochi ingredienti, ma di qualità: una corretta distribuzione dei prodotti in funzione degli indici e dei KPI, una scelta coerente dei sistemi di stoccaggio in virtù dell'unità di carico da conservare, una buona predisposizione delle aree in cui si svolgono i processi intermedi. Infine, in un contesto sempre più caratterizzato da flussi logistici complessi, a cui si sommano la gestione dei resi e-commerce e dei lead time ridotti, anche il software WMS diventa un elemento essenziale per far sí che durante il fluire dei prodotti nulla si perda per strada.