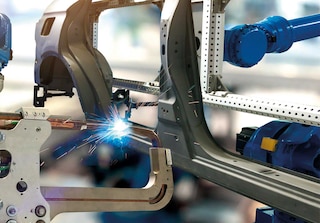
Sistema MRP per la pianificazione dei fabbisogni di materiali
La pianificazione dei fabbisogni materiali per il processo di produzione è un’operazione logistica complessa. Di quante materie prime ho bisogno? Quando ne ho bisogno? Quante unità produrre? Questi sono solo alcuni dei quesiti che da decenni possono essere risolti grazie al sistema MRP (Material Requirements Planning).
In questo post analizzeremo tutto ciò che riguarda la pianificazione del fabbisogno di materiali: cos'è, come funziona, quali vantaggi apporta e perché è stato ed è così importante nel processo produttivo, ma anche per quel che riguarda l'operatività del magazzino. In aggiunta a tutto ciò, approfondiremo la differenza tra un sistema MRP e un ERP.
Cos’è l’MRP?
La pianificazione dei fabbisogni materiali o Material Requirements Planning è un sistema progettato per gestire e coordinare i processi di produzione, acquisto e consegna del prodotto finito.
Il sistema MRP è nato negli anni '70 e la sua crescita è stata rapida. Nel 1975 erano già 700 le aziende che avevano adottato il sistema MRP per ottimizzare i propri processi produttivi. Questo dato è contenuto neñ libro Production Planning and Control: A Comprehensive Approach scritto da D.R. Kiran nello stesso periodo. Una cifra che è aumentata ogni anno del 174%, fino a raggiungere quota 8.000 aziende nel 1981, dopo appena sei anni.
Oggi il sistema MRP è considerato il capostipite dei moderni programmi informatici dedicati al miglioramento dei processi industriali: MRP II (Manufacturing Resource Planning), ERP (Enterprise Resource Planning), CRM (Customer Relationship Management), SRM (Supplier Relationship Management) o MES (Manufacturing Execution System).
L’MRP organizza le attività di produzione e ottimizza la gestione delle scorte in base alle esigenze dell'azienda. Con il supporto di questo modulo, i produttori possono raggiungere il loro obiettivo principale: disporre sempre di un material planning accurato e consegnare i prodotti ai clienti in tempi ridotti e al minor costo possibile.
Come funziona un MRP?
Il sistema MRP richiede si fonda sui seguenti elementi essenziali (input):
- Piano di produzione principale: noto come MPS (Master Production Schedule) e in cui si mostrano sia i quantitativi di articoli che verranno prodotti sia gli intervalli di produzione.
- BOM (Bill of materials): la distinta base, ovvero la lista di materie prime necessarie per la produzione del prodotto finale.
- Catalogo e inventario: in questi sono contenute le informazioni relative allo stock (inventario disponibile, stock richiesto, ordini annullati, tempi di attesa, ecc.). Servono a monitorare la disponibilità di materie prime.
Il sistema di pianificazione del fabbisogno di materiale trasforma questi input nei seguenti output:
- Piano di produzione principale raccomandato: si tratta di un calendario che include le date relative al processo di produzione (inizio e fine), le quantità per ogni fase del ciclo e la distinta base (BOM). Il suo obiettivo è soddisfare la domanda specificata nel piano di produzione principale.
- Programma di acquisto consigliato: mostra le date di ricezione dei materiali acquistati, nonché le date in cui devono essere emessi gli ordini relativi al piano di produzione.
Il sistema MRP si occupa del monitoraggio delle scorte e di mantenere un livello minimo di inventario per fornire i processi produttivi. Ne scaturisce pertanto una pianificazione più efficiente delle attività di produzione, acquisto e consegna dei materiali.
Esempio di pianificazione dei requisiti dei materiali
Dopo aver realizzato il piano di produzione principale e la distinta base, si determina che per realizzare un prodotto finale (prodotto X), sono necessarie 2 unità di materiale A e 1 unità di materiale B. Per ogni unità di materiale A, sono necessarie 3 unità di materiale C e per ogni unità di materiale B, sono necessarie 2 unità della parte C e 4 unità della parte D.
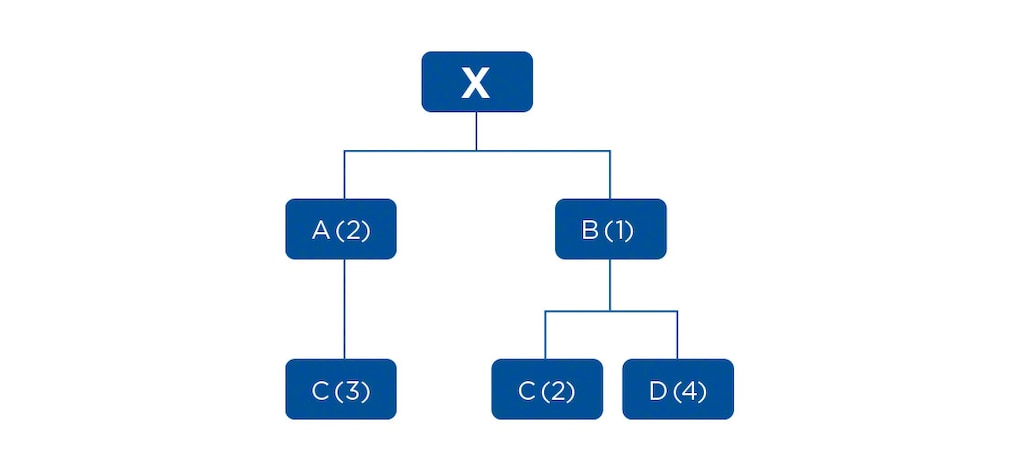
Il seguente passo sarà pertanto completare il file IRF (Inventory Record File), in cui si riflette l'inventario disponibile e il tempo di consegna necessario per ricevere ciascun prodotto:

Una volta completato questo passaggio, si ottiene la pianificazione del fabbisogno di materiali. Pertanto se volessimo produrre 100 unità di prodotto X in 10 settimane, il nostro documento si presenterebbe così:
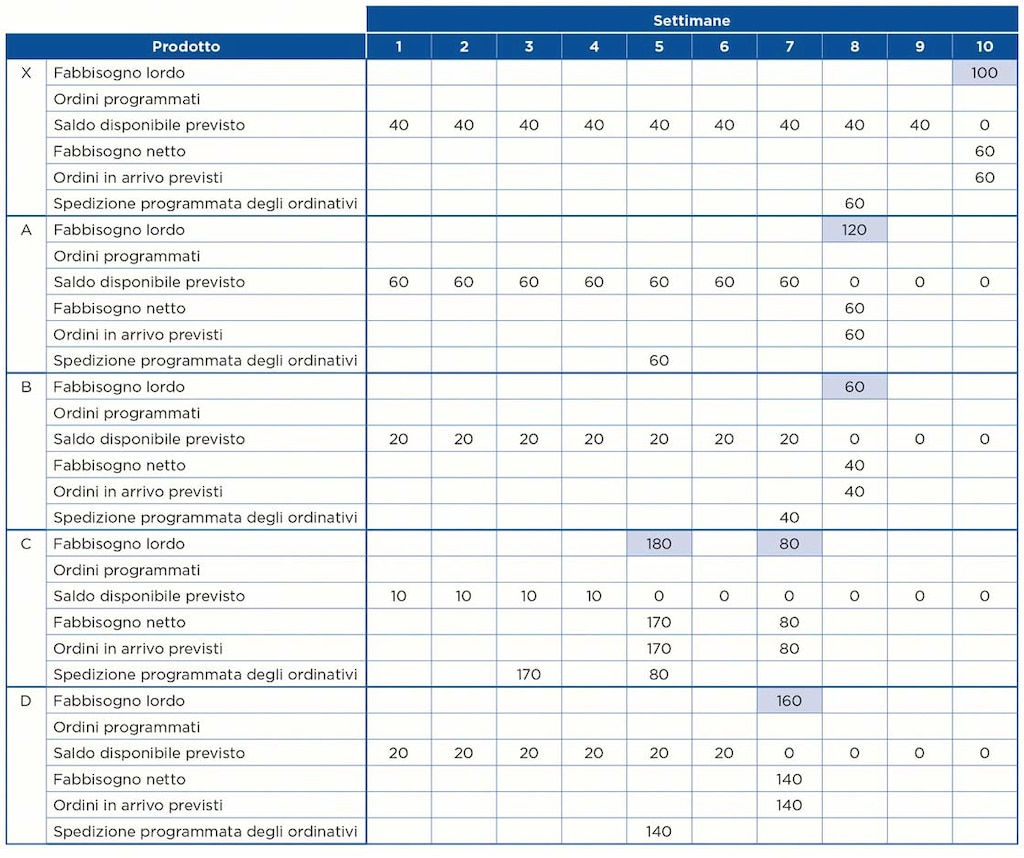
Dalla tabella si evince che per avere 100 unità del prodotto X nella settimana 10 sono necessarie 60 unità aggiuntive, oltre alle 40 unità già disponibili in magazzino. Dato che nel registro dell'inventario abbiamo definito che il lead time per il prodotto X è di 2 settimane, l'ordine dovrà essere effettuato nella settimana 8.
Se sono necessarie 2 unità di prodotto A per ciascuna unità di prodotto X, allora per la settimana 8 saranno richieste 120 unità di prodotto A. Dato che 60 unità sono già in magazzino, il fabbisogno netto di prodotto A corrisponderà a 60 unità, dunque queste unità dovranno essere richieste con tre settimane di anticipo, tenendo conto dei tempi di attesa.
Seguendo lo stesso criterio, è possibile elaborare il material planning dei prodotti B, C, D e F, nonché determinare la settimana in cui devono essere richiesti.
Funzioni e vantaggi di un MRP
All'interno di un processo produttivo, la pianificazione del fabbisogno di materiali ha la funzione di calcolare le materie prime e i componenti necessari per ottenere un prodotto finito.
Esistono anche una serie di vantaggi collegati all’MRP, elenchiamo qui di seguito i principali:
- Totale disponibilità di materia prima per la produzione.
- Rispetto delle scadenze.
- Mantenere bassi livelli di giacenze, sia per le materie prime che per i prodotti finiti.
- Pianificazione accurata delle attività di produzione, ordini di consegna e acquisti.
- Riduzione dei costi.
Inoltre il sistema MRP agevola le fasi di acquisto ottimizzando l’approvvigionamento delle materie prime. Si evitano pertanto sia gli ordini di acquisto errati o insufficienti che potrebbero ritardare i tempi di consegna e fermare la produzione, sia gli ordinativi in eccesso che comporterebbero costi extra di stoccaggio.
Differenze tra MRP e MRP2
All'inizio degli anni '80, il sistema MRP (Material Requirements Planning) si è evoluto in MRP 2 (Manufacturing Resource Planning), un sistema di pianificazione più avanzato con un ventaglio di funzionalità più ampio. Le principali differenze tra i due sistemi sono:
- Oltre a pianificare il fabbisogno di materiali necessari alla produzione, l'MRP2 è in grado di integrare altri reparti aziendali, come quello commerciale, finanziario, ecc.
- Il funzionamento dell’MRP si basa sul piano di produzione principale, invece l’MRP2 si basa sullo studio della domanda e del mercato.
- L'MRP2 analizza l’andamento delle performance aziendali per eseguire una pianificazione efficiente, a differenza dell'MRP che lo fa attraverso la pratica e la precedente esperienza dell'azienda.
- L'MRP è un sistema aperto al contrario dell'MRP2. Ciò significa che l'MRP2 riesce a ottenere feedback dai report che genera, rielaborando così dati più in linea con la realtà.
L'MRP2 è la versione modernizzata dell'MRP. Oltre a determinare quanto e quando produrre, definisce anche di quali risorse disporre per realizzare i processi produttivi.
Differenze tra MRP ed ERP
Il sistema ERP (Enterprise Resource Planning) è stato utilizzato per la prima volta negli anni Novanta, delineandosi come una versione più completa e versatile dei suoi predecessori MRP. In effetti, l’ERP è un sistema in grado di raccogliere e centralizzare i dati provenienti dai processi da tutte le aree dell'azienda.
In altre parole, l’MRP è un software che funziona da solo, mentre l’ERP integra e combina i sistemi informatici utilizzati da ogni reparto aziendale creando un database unico. In questo modo qualsiasi area aziendale può: accedere alle informazioni in tempo reale, monitorare i flussi di lavoro, ridurre al minimo gli errori di gestione e comunicare con gli altri reparti.
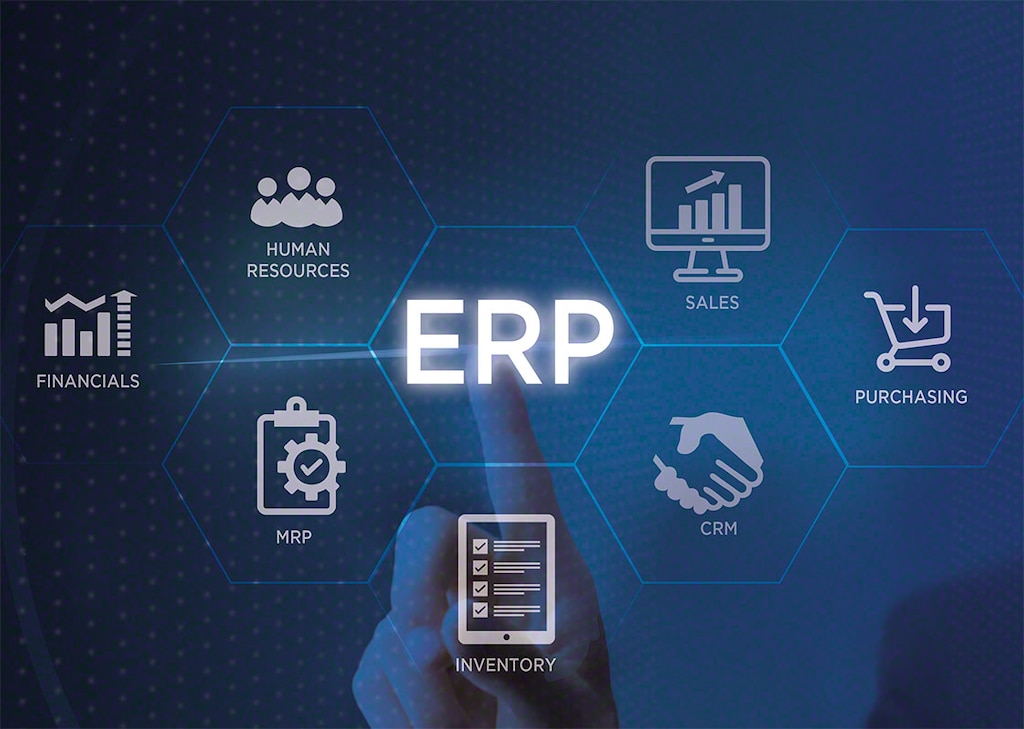
MRP: la pianificazione dei fabbisogni di materiali sulla scia dei progressi tecnologici
Dopo quasi di cinquant'anni di MRP si può affermare affermare che la pianificazione dei requisiti materiali ha segnato un prima e un dopo nei processi di produzione. La capacità di pianificazione, intesa come il saper anticipare le esigenze, è stata adattata alle nuove tecnologie in un'ottica di miglioramento della redditività della filiera.
In Mecalux puntiamo sempre sulle soluzioni tecnologiche più innovative del mercato, sia per lo stoccaggio che per la gestione della logistica, come avviene con Easy WMS. Questo sistema può essere integrato con qualsiasi ERP, conferendo un maggiore controllo e capacità di reazione nella gestione delle scorte e, quindi, una maggiore produttività in magazzino.
Se sei alla ricerca di un partner affidabile per portare al top la performance del tuo centro, contattaci: i nostri esperti saranno lieti di illustrarti le soluzioni più idonee per la tua supply chain.