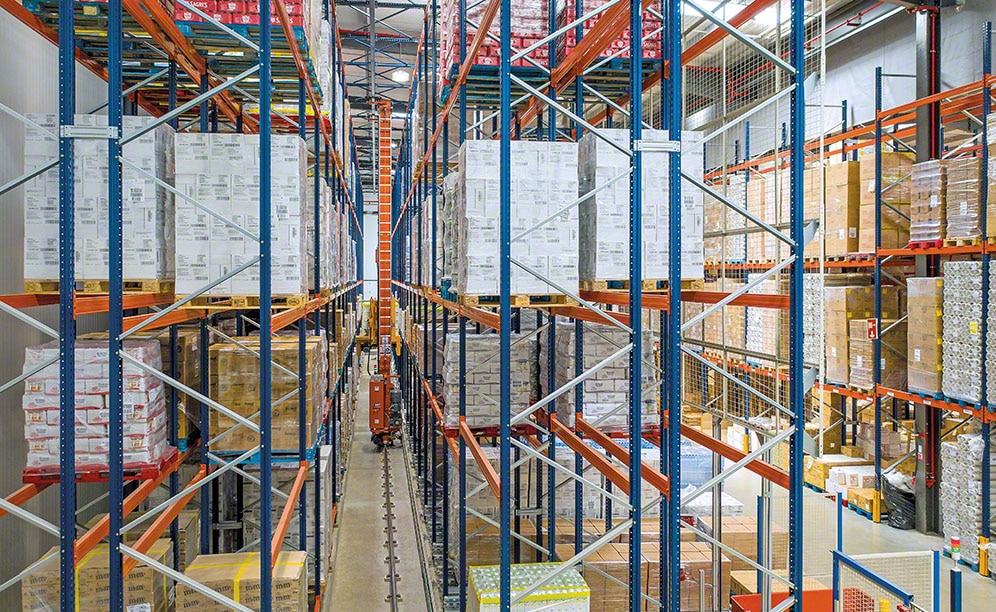
Tecnologia per migliorare la produttività, l’efficienza e il consumo energetico
La cella di congelamento completamente automatica di HAVI dove stocca i prodotti alimentari
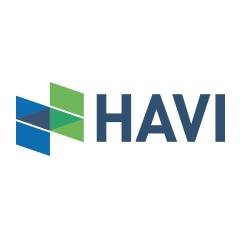
HAVI ha inaugurato un centro logistico moderno e tecnologicamente avanzato in Portogallo da cui rifornisce i clienti del settore alimentare nel Paese. Il centro è diviso in tre aree che operano a temperatura ambiente, refrigerata e a -20 °C. Mecalux ha fornito tutti i sistemi di stoccaggio: due magazzini automatici, scaffalature portapallet, drive-in e il sistema Pallet Shuttle . Inoltre, ha implementato Easy WMS, il Software Gestione Magazzino collegato al WMS di HAVI per controllare lo stock e garantire il sequenziamento della spedizione della merce.
A proposito di HAVI
HAVI è una multinazionale che innova e ottimizza la supply chain di marchi leader. Il catalogo dei servizi offre analisi, logistica, gestione della supply chain e imballaggio. Fondata nel 1974, HAVI è presente in più di cento Paesi. In Portogallo, tra i clienti del settore alimentare comprende la popolare catena di fast food McDonald’s e Portugalia.
Tra i punti di forza di HAVI risaltano l’efficienza operativa e l’eccellenza nel campo dei servizi e in materia di sicurezza e qualità. Si tratta di un’azienda all’avanguardia nella fornitura puntuale di prodotti per la ristorazione. In quest’ottica, i suoi centri logistici sono organizzati con un ciclo operativo dinamico ed efficiente che controlla integralmente la merce nel rispetto delle corrette condizioni di conservazione.
Un magazzino moderno,efficiente e sostenibile
Il team tecnico di Mecalux ha collaborato ancora una volta con HAVI per progettare, costruire e avviare un moderno centro logistico a Vila Nova da Rainha (Portogallo). Da questo centro di distribuzione, HAVI rifornisce i clienti del settore della ristorazione di tutto il Paese. Le due multinazionali avevano collaborato su progetti precedenti, formando un binomio di successo. Ad esempio, Mecalux aveva installato un magazzino automatico per HAVI a Mosca (Russia); inoltre aveva attrezzato con scaffalature su basi mobili Movirack il centro che l’azienda possiede a Lodi (Italia).
Il nuovo centro di HAVI in Portogallo si estende su una superficie totale di 10.000 m² ed è suddiviso in tre aree che permettono di stoccare e conservare la merce alla giusta temperatura: congelamento, refrigerazione e ambiente. Ciascuna delle celle ha una distribuzione specifica che segue le esigenze logistiche dell’azienda. Per questo motivo, Mecalux ha installato diverse soluzioni di stoccaggio e picking (automatiche e portapallet).
Operatività e affidabilità nella gestione dello stock sono il denominatore comune di queste soluzioni che, insieme, rendono più dinamiche le attività di stoccaggio e preparazione degli ordini. Questo centro, oltre ad essere un punto di riferimento a livello tecnologico, è altresì un precursore in termini di automazione dei processi logistici a -20 °C.
Le scaffalature portapallet sono state installate in tutte e tre le aree del centro. La scelta è dovuta dal fatto che si adattano a qualsiasi tipo di carico variabile per peso e volume. In più, l’accesso diretto agevola la gestione della merce. Ai livelli inferiori, gli operatori effettuano il picking direttamente dai pallet con l’ausilio di terminali a radiofrequenza, mentre ai livelli superiori delle scaffalature viene depositata la merce di scorta.
Nella progettazione di tutte le soluzioni di stoccaggio, Mecalux ha dato priorità alla sicurezza, della merce e degli operatori. Il rispetto della catena del freddo per evitare che questa si spezzi è fondamentale. Pertanto gli accessi alla cella refrigerata e di congelamento sono isolati per evitare bruschi sbalzi di temperatura, perdita di freddo e condensazioni.
Anche l’automazione ha contribuito ad aumentare la sicurezza, poiché il 77% delle movimentazioni dei pallet si svolge in modo assolutamente automatico. Inoltre, l’ergonomia durante la movimentazione dei prodotti è stata ottimizzata e lo sforzo fisico ridotto. E’ necessario sottolineare inoltre che i lavoratori trascorrono meno tempo in ambienti freddi. In tal modo, oltre a migliorare la qualità del lavoro, si riduce del 10% il consumo energetico evitando di aprire troppo spesso le porte di accesso alla cella.
Rappresentante di HAVI
“Ora siamo in grado di seguire le variazioni nelle attività dell’azienda, controlliamo meglio il periodo di conservazione dei prodotti alimentari e gestiamo gli ordini con maggiore efficienza”.
Cella di congelamento
La cella è attrezzata con il moderno sistema Pallet Shuttle automatico assistito da due trasloelevatori e gestito con Easy WMS. Qui si stoccano le referenze ad alta rotazione come, ad esempio, hamburger, patate o prodotti a base di pollo. “Una buona parte degli ordini inviati ai ristoranti viene preparata nella cella di congelamento”, afferma un responsabile di HAVI. Il magazzino, che opera a una temperatura di -20 °C, è dotato di due corsie con due blocchi di scaffalature che hanno una profondità massima di sei pallet. Complessivamente, offrono una capacità di stoccaggio di 2.247 posti pallet, vale a dire circa il 75% in più rispetto a un sistema di stoccaggio non automatico.
Il sistema Pallet Shuttle automatico ottimizza lo spazio di stoccaggio e riduce il volume da raffreddare. In questo modo, è possibile sfruttare al massimo la capacità di stoccaggio e risparmiare al contempo sul costo energetico necessario affinché l’impianto operi a temperature inferiori allo zero. “Il nostro obiettivo era migliorare l’efficienza di quest’area e, al tempo stesso, le condizioni dei dipendenti”, sottolinea un rappresentante di HAVI.
Il ciclo operativo è completamente automatico, essendo presenti due trasloelevatori bicolonna che trasportano la merce dalle postazioni in entrata e in uscita del magazzino ai livelli di carico. All’interno dei canali, inoltre, navetta effettua la movimentazione della merce. L’intero ciclo si svolge sotto la supervisione di Easy WMS che ha il compito di controllare lo stock del magazzino. Il software comunica con il WMS di HAVI al fine di garantire la totale tracciabilità della merce, dal ricevimento alla consegna ai clienti. Di fianco al magazzino è stato installato un circuito di trasportatori che trasferisce la merce all’area di picking a una velocità costante di 20 m/min, secondo il principio “merce all’uomo”. “Grazie a questo metodo di preparazione degli ordini, abbiamo migliorato le condizioni di lavoro”, osserva uno dei responsabili di HAVI. Easy WMS effettua il sequenziamento degli ordini che vengono preparati singolarmente o insieme in due postazioni di picking manuale e in una di picking automatico, a seconda dell’ordine. A tal fine, una navetta collega le tre postazioni di picking tra loro e con la zona di avvolgimento con pellicola termoretraibile e di etichettatura.
La postazione di picking automatico è provvista di un robot antropomorfo che movimenta numerosi pallet di prodotti ad alta rotazione, che rappresentano il 40% del volume totale degli ordini preparati nella cella di congelamento. Il grande vantaggio di questo tipo di macchine è la velocità; possono infatti preparare vari ordini simultaneamente. Il picking automatico offre velocità e risparmio dei costi operativi, soprattutto nelle celle di congelamento.
Le due postazioni di picking manuale ricevono automaticamente la merce dai trasportatori provenienti dal magazzino o dalla navetta, nel caso in cui sia passata precedentemente attraverso il robot antropomorfo. In entrambi i casi, il principio “merce all’uomo” consente di ridurre gli spostamenti e di velocizzare la preparazione degli ordini. Ogni postazione è dotata di dispositivi luminosi PTL (pick-to-light), l’operatore può così preparare in modo ergonomico fino a otto ordini simultaneamente con conseguente ottimizzazione della produttività e della qualità del lavoro. Easy WMS comunica con gli operatori attraverso un monitor che indica le attività da svolgere per mantenere il sequenziamento degli ordini: i prodotti da prelevare, a quale ordine corrispondono e così via. Una volta completato il lavoro, gli operatori trasmettono le informazioni al WMS premendo il dispositivo PTL.
Successivamente, la navetta preleva gli ordini e li invia alla fasciatrice e all’etichettatrice. I trasportatori poi li trasferiscono fino all’area spedizioni in modo sequenziale. L’area in questione, anch’essa a temperatura controllata per non spezzare la catena del freddo, è formata da otto canali a gravità di precarico dove i pallet vengono classificati e raggruppati in base all’ordine o all’itinerario di trasporto. Il rispetto del sequenziamento e il raggruppamento anticipato degli ordini nei canali di precarico contribuiscono a risparmiare tempo e a ridurre al minimo gli errori durante il carico della merce sul camion.
Nella cella di congelamento è stato installato anche un blocco di scaffalature a stoccaggio intensivo con il sistema Pallet Shuttle semiautomatico che ha una capacità di 237 posti pallet. Contengono soprattutto pane.
Questa soluzione, che tra l’altro ottimizza la superficie di stoccaggio, è dotata di una navetta che movimenta automaticamente i pallet all’interno dei canali, ma a differenza di quanto avviene con il magazzino automatico, gli operatori, servendosi di carrelli retrattili, depositano la navetta e la merce nel canale corrispondente.
Cella refrigerata
Oltre alle scaffalature portapallet, Mecalux ha installato un blocco di scaffalature drive-in alte 9 m con una capacità di stoccaggio di 1.996 posti pallet. Si tratta di una soluzione ottimale per lo stoccaggio di prodotti omogenei che hanno una grossa quantità di pallet per referenza come, ad esempio, pomodori o insalate pronte.
Le scaffalature sono formate da un insieme di tunnel a quattro livelli di altezza. Inoltre, ogni livello è dotato di binari GP ai due lati su cui vengono depositati i pallet. Per gestire la merce, gli operatori, sui carrelli retrattili, entrano nei tunnel con il carico sollevato al di sopra del binario GP su cui sarà depositato.
Celle a temperatura ambiente
In quest’area, destinata a prodotti quali ketchup, maionese o bottiglie d’acqua e di altre bevande, si trova un magazzino automatico con una capacità di 530 posti pallet pallet formato da un’unica corsia con scaffalature a doppia profondità alte 10,2 m ai due lati. Un trasloelevatore bicolonna sposta i prodotti lungo la corsia dai trasportatori in entrata alle ubicazioni assegnate dal WMS.
Sul livello inferiore delle scaffalature sono stati predisposti 36 canali a gravità per picking che corrispondono con la corsia di lavoro. Ogni canale può contenere quattro pallet della stessa referenza: uno per il picking e gli altri di scorta. Gli operatori, attraverso terminali a radiofrequenza, localizzano le referenze comprese nei singoli ordini ed effettuano il picking dal primo pallet.
Quando il pallet di un canale a gravità rimane sprovvisto di merce, il WMS trasmette l’ordine di riassortimento. Il vantaggio di questo sistema è che i prodotti necessari per il picking sono sempre disponibili, evitando così interruzioni e ritardi nella preparazione degli ordini.
Easy WMS: sequenziamento e controllo della merce
I due magazzini automatici di HAVI (quello della cella di congelamento e l’altro della cella a temperatura controllata) sono coordinati dal Software Gestione Magazzino Easy WMS di Mecalux. Nel magazzino automatico con Pallet Shuttle, Easy WMS identifica gli articoli quando arrivano in magazzino e assegna loro un’ubicazione sulla base dell’impilabilità e del tipo di merce. Il sistema offre totale tracciabilità, consentendo di conoscere in tempo reale l’esatta ubicazione di tutta la merce. Il software inoltre organizza la preparazione degli ordini. Trasmette infatti l’ordine di inviare le referenze richieste alle postazioni di picking e indica agli operatori i prodotti compresi nell’ordine. Easy WMS svolge tutte queste attività tenendo conto di uno dei requisiti principali di HAVI, ossia il sequenziamento degli ordini. Il raggruppamento e il sequenziamento della merce per la spedizione eliminano gli errori, velocizzano il ciclo operativo e consentono di offrire un servizio più efficiente.
Inoltre, nella cella a temperatura ambiente Easy WMS coordina i movimenti del trasloelevatore. La sua funzione è di di rifornire di merce i canali di picking dinamico mentre si svuotano. Easy WMS comunica con il software di HAVI allo scopo di controllare lo stock, conoscere la tracciabilità e sequenziare tutti i processi del centro di distribuzione.
Tecnologia al servizio dei clienti
HAVI vanta un centro di distribuzione moderno e tecnologico con un ciclo operativo efficiente, pronto per rifornire i ristoranti dei clienti in base alle richieste. L’automazione non si è limitata a rendere più dinamici i flussi del magazzino, ma ha anche permesso di ridurre i costi logistici e ottimizzare il lavoro degli operatori. Da sottolineare anche che questo impianto ha consentito agli operatori di HAVI di sviluppare nuove competenze.
Vantaggi per HAVI
- Classificazione della merce: il magazzino è stato settorizzato in tre aree in cui sono state installate soluzioni diverse per stoccare e gestire la merce in base alle caratteristiche.
- Sequenziamento degli ordini: Easy WMS sequenzia gli ordini pronti e li invia all’area di precarico, dove vengonono classificati in base all’ordine o all’itinerario di trasporto.
- Tecnologia e sicurezza: grazie all’automazione, il magazzino rispetta i requisiti fondamentali in materia di sicurezza per quanto riguarda la merce e gli operatori.
- Luogo di lavoro gratificante: HAVI ha modernizzato l’ambiente di lavoro rendendolo più piacevole per gli operatori, garantendo l’opportunità di ampliare le competenze attraverso l’uso di nuove tecnologie.
Centro logistico in Portogallo: Scaffalature portapallet | |
---|---|
Capacità di stoccaggio: | 6.341 posti pallet |
Dimensioni dei pallet: | 800 x 1.200 mm |
Peso massimo dei pallet: | 1.000 kg |
Altezza delle scaffalature: | 8,5 m |
Galleria
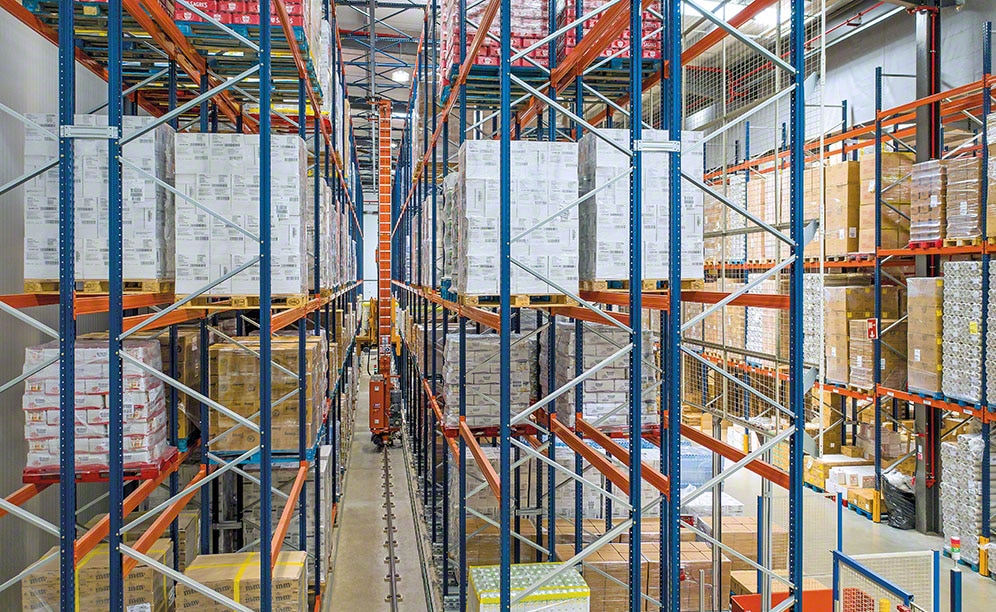
Sistema Pallet Shuttle con trasloelevatore di HAVI in Portogallo
Consultate un esperto