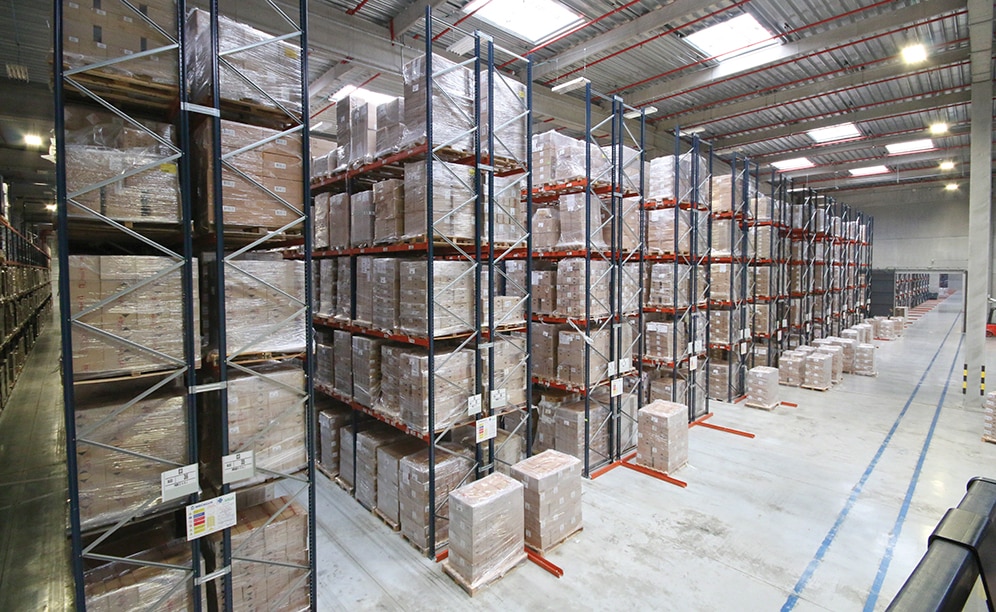
Un magazzino suddiviso in settori per SAGA
Un circuito di picking completo per l’azienda francese di trasporto e logistica SAGA
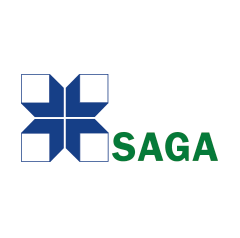
Con una capacità di stoccaggio totale che supera i 42.000 posti pallet, nel magazzino di SAGA a Saint-Priest assume un ruolo importante l’area specifica di picking, dato che l’azienda ha bisogno di estrema agilità per rispondere alle richieste della sua rete di uffici presenti in più di 100 Paesi. Questa zona di picking, formata da scaffalature a gravità e portapallet, soddisfa tutte le esigenze di SAGA e ne riduce i costi di gestione.
Un magazzino strutturato
Il magazzino di SAGA è suddiviso in cinque zone indipendenti isolati tra loro come misura di prevenzione antincendio. Su ognuno di esse sono state installate scaffalature portapallet: le zone 1, 2 e 3 vengono servite da carrelli elevatori di tipo trilaterale, mentre nelle altre due si lavora con carrelli retrattili.
Inoltre, in queste ultime due zone si stoccano e preparano prodotti che vengono preparati nell’area specifica di picking, installata nella zona 5.
Questi elementi non sono necessari nelle scaffalature servite da carrelli retrattili, tuttavia sono state predisposte delle protezioni montanti e laterali spalla che consentono di prevenire possibili impatti, come è possibile vedere nella fotografia a destra.
Zona di picking: processo da seguire per la preparazione degli ordini
- 1.- La formatrice automatica di scatole crea scatole della dimensione necessaria a partire da cartone piatto di formati diversi.
- 2.-Le scatole formate vengono accumulate in un circuito a “U” ed entrano nel circuito principale man mano che sono necessarie. Successivamente, viene applicata automaticamente l’etichetta d’identificazione.
- 3.- Le scaffalature di picking a gravità, ubicate all’inizio del circuito, si trovano sui lati delle due corsie, permettendo di stoccare più di un centinaio di referenze di tipo A distribuite su 48 campate. Sotto le scaffalature di picking e tra due livelli di stoccaggio, circola il convogliatore continuo per gli ordini già completati. Al suo fianco, si trova un altro convogliatore non automatizzato che funge da piattaforma di preparazione.
- 4 e 5.- Il circuito di convogliatori percorre le due corsie precedenti. Uno dei moduli è basculante, rendendo possibile il passaggio di persone e navette nell’area successiva.
- 6.- In questa seconda zona vengono preparati i prodotti di tipo B e C. A tale scopo, sono state adibite 36 campate di scaffalature a gravità e 112 campate bifronti di scaffalature portapallet.
- 7.- Gli ordini, dopo essere stati preparati, vengono condotti fino alla postazione di verifica e controllo del peso, dove si accerta che non vi siano errori e che l’ordine sia stato completato.
- 8.- Nell’area di imballaggio si posizionano e proteggono i prodotti prima che vengano trasferiti alle varie macchine che chiudono e reggiano le scatole. A questo punto, si stampano le bolle di consegna che vengono inserite all’interno delle scatole e si applicano manualmente le restanti etichette necessarie per la spedizione.
- 9.- Questa zona dispone di 12 canali di classificazione automatica degli ordini, che corrispondono a diverse destinazioni di spedizione.
L’area di picking è composta delle seguenti parti:
- Formatrice di scatole di cartone.
- Convogliatori di identificazione e accumulo di scatole vuote.
- Scaffalature a gravità per scatole (destinate a prodotti ad alta rotazione) combinate a convogliatori.
- Convogliatori per scatole.
- Campata basculante per permettere il passaggio tra le varie zone.
- Zona di scaffalature a gravità per prodotti a media rotazione (tipo B) e portapallet per prodotti a bassa rotazione (tipo C).
- Verifica degli ordini preparati, zona di imballaggio, emissione delle bolle di consegna, etichettatura e reggiatura.
- Zona di classificazione degli ordini.
Preparazione degli ordini
Ogni volta che si lancia un nuovo ordine, l’SGM (Sistema di Gestione del Magazzino) indica all’accumulatore la quantità e dimensione delle scatole necessarie.
In seguito, l’etichettatrice automatica applica alla scatola le etichette con il relativo codice a barre. L’operatore preleva le scatole e ne legge il codice mediante il terminale a radiofrequenza affinché il sistema indichi la tipologia e la quantità della merce da prelevare.
Il magazzino è suddiviso in varie zone e un operatore è assegnato a ognuna di esse. Quando il primo operatore ha preparato la parte che gli corrisponde, trasferisce la scatola al successivo operatore affinché prosegua con il processo. Man mano che si completano gli ordini o si vanno riempiendo le scatole, vengono introdotti nel convogliatore automatico che passa all’interno delle scaffalature.
Benché il circuito continuo è a “U”, le scatole che hanno bisogno di prodotti a media e bassa rotazione vengono deviate a un convogliatore a gravità in attesa che l’operatore assegnato a questa zona inizi a preparare queste referenze.
L’operatore della zona B e C utilizza una navetta che può portare sei scatole corrispondenti a sei ordini diversi.
Il processo si conclude con il trasferimento manuale di queste scatole ai relativi pallet e infine con la loro spedizione.
La grande capacità del magazzino, la sua suddivisione in settori e specializzazione, così come l’ubicazione delle baie di carico e la flessibilità ottenuta con i sistemi di stoccaggio e picking installati, permettono a SAGA di offrire ai suoi clienti un servizio efficace e rapido.
Vantaggi per SAGA
- Alta capacità di stoccaggio: il magazzino di SAGA è in grado di stoccare più di 42.000 pallet su una superficie di 48.000 m2.
- Aumento della velocità di preparazione degli ordini: un circuito di picking efficiente ottimizza i movimenti durante la preparazione degli ordini ad alta, media e bassa rotazione.
- Riduzione dei costi: ogni settore dispone delle proprie baie di carico, ciò evita grandi spostamenti e riduce notevolmente i costi di gestione.
Magazzino di SAGA | |
---|---|
Capacità di stoccaggio: | 42.410 posti pallet |
Peso massimo per pallet: | 800 kg |
Dimensioni del pallet: | 800 x 1.200 mm |
Altezza del magazzino: | 9 m |
Galleria
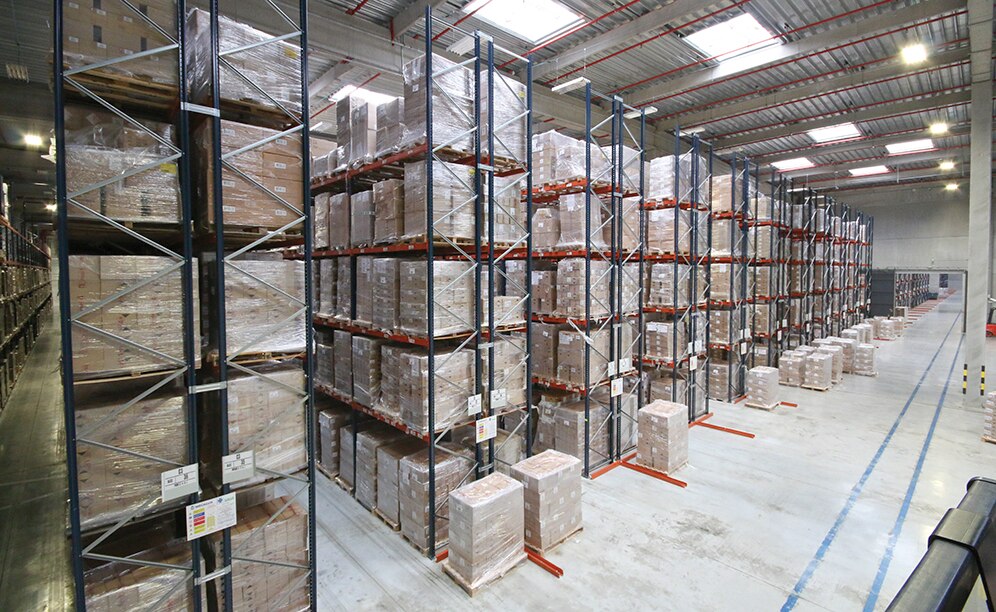
Consultate un esperto