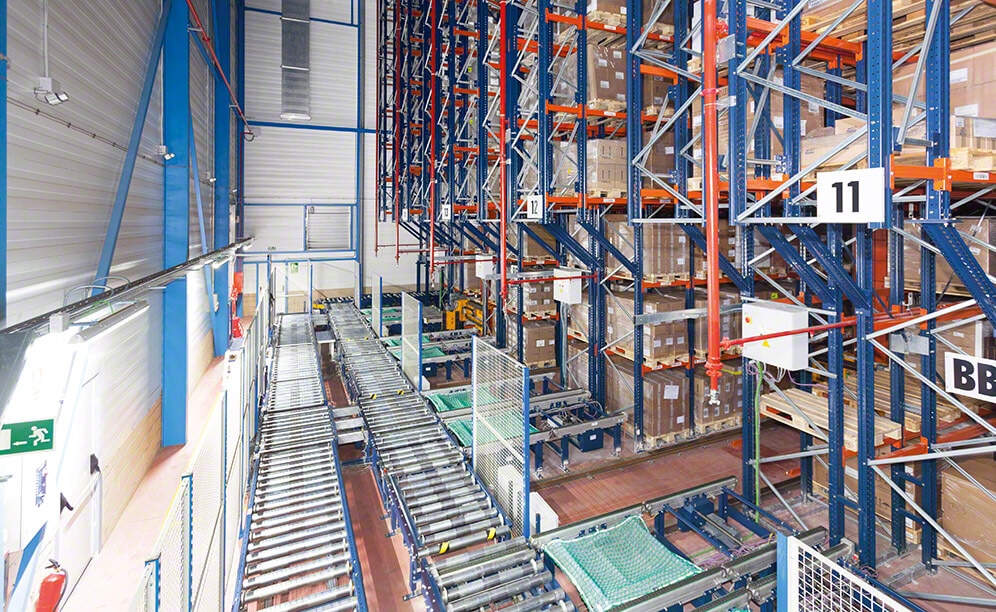
Disalfarm ottiene capacità, produttività e controllo con l'automazione in diverse fasi del suo magazzino portapallet
Disalfarm automatizza il suo magazzino in maniera semplice ed economica con trasloelevatori trilaterali

Il centro logistico, presso le strutture che Disalfarm possiede a Rubí (Barcellona), è stato costruito su una superficie di 39.027 m². Il magazzino, completamente automatico e con una capacità di stoccaggio di oltre di 19.000 posti pallet, ha migliorato notevolmente la produttività dell'azienda. Tutto ciò, senza mai smettere di funzionare durante l'ampliamento e la modernizzazione del magazzino.
A proposito di Disalfarm
Disalfarm S.A. è un'azienda di logistica fondata in Spagna dai laboratori Bayer, Boehringer Ingelheim e Novartis con lo scopo di concentrare le proprie operazioni nazionali, sia di stoccaggio sia di distribuzione di specialità farmaceutiche.
L'azienda ha avviato le sue attività nel 2000, con l'ambizione di diventare leader nel settore della distribuzione farmaceutica.
A tale scopo, era indispensabile lavorare con un sistema di qualità che organizzasse le norme di corretta produzione e distribuzione richieste dalla legislazione vigente.
Oggi, Disalfarm vanta un'ampia gamma di prodotti, dalle specialità farmaceutiche di prescrizione medica ai farmaci di uso ospedaliero e veterinario, integratori alimentari e altri prodotti sanitari.
Dove si trova?
Disalfarm, S.A. è situata nella città di Rubí, una zona industriale vicino a Barcellona che costituisce un importante snodo di comunicazioni.
I suoi impianti sono in prossimità dei principali centri logistici e di distribuzione, potendo così offrire un servizio rapido ed efficiente a tutti i clienti.
Esigenze di Disalfarm: migliorare senza ridurre il servizio
La crescita sperimentata da Disalfarm negli ultimi anni ha modificato sostanzialmente le sue esigenze di stoccaggio.
Nel 2000 è stato costruito un centro logistico che combinava le operazioni di stoccaggio con quelle di picking: meno del 20% degli ordini corrispondeva a pallet completi con una sola referenza.
In questa prima fase sono stati creati anche due capannoni riservati al magazzino, una zona di preparazione e consolidamento, le baie di carico e scarico e, infine, gli uffici e i servizi.
L'insieme di queste strutture occupava una superficie di 9.706 m2. Tutte le scaffalature del magazzino e la zona di picking sono state installate da Mecalux.
Nel 2007 il magazzino propriamente detto si è rivelato insufficiente a soddisfare le esigenze dell'azienda. L'elevato numero di movimenti effettuati dai carrelli di movimentazione presupponeva un costo smisurato e, al contempo, aumentava il rischio di incidenti sul lavoro, situazione incompatibile con i principi di Disalfarm.
La grande sfida che l'azienda ha proposto a Mecalux è stata, quindi, di aggiornare questo centro logistico senza alterare il servizio ai clienti.
Punto di partenza: fase 1 e fase 2
Nella prima fase, realizzata nel 2000, è stato costruito:
- Un magazzino con una capacità di 12.900 pallet da 800 x 1.200 mm formato da dieci corsie con scaffalature da 15 m di altezza.
- Zona di picking composta da scaffalature a gravità con dispositivi pick-to-light e rulliere per contenitori che mettevano in comunicazione quest'area con quella di imballaggio e consolidamento.
- Zona di picking di contenitori completi che si effettua direttamente sui pallet.
- Magazzino per prodotti refrigerati con una capacità di 290 posti pallet.
- Magazzino chiuso per prodotti psicotropi.
- Nove baie di carico con un'ampia zona di manovra.
Nella seconda fase, sono state aggiunte altre cinque corsie con scaffalature portapallet con una capacità di 6.450 posti pallet, per un totale di 19.350 posti pallet.
Inoltre, sono state terminate tre nuove baie di carico.
Anche il flusso di movimentazioni è stato incrementato considerevolmente, fino a raggiungere i 1.100 pallet al giorno (500 in entrata e 600 in uscita).
Per poter movimentare questo numero di pallet, si utilizzavano le seguenti risorse:
- Sette carrelli di carico frontale per lavorare nelle baie, alimentare le zone di picking e depositare e prelevare i pallet dalla testata delle corsie.
- Cinque carrelli trilaterali per lavorare solo all'interno delle corsie di stoccaggio.
- 24 operatori per manovrare i carrelli (12 per turno).
Nei due grafici di questa sezione si osserva come i flussi di movimentazione (entrate e uscite) si incrociano nella corsia principale.
Flusso della merce nelle fasi 1 e 2La merce arrivava al magazzino completamente pallettizzata. L'operatore leggeva il codice a barre di ciascun pallet con un terminale informatico e il sistema di gestione del magazzino (SGM) gli indicava a quale corsia era assegnato. Una volta determinata la posizione, si utilizzavano i carrelli frontali per portare i pallet alle mensole collocate all'estremità della corsia di stoccaggio, affinché i carrelli trilaterali li stoccassero nelle ubicazioni previste dal sistema di gestione.
Le operazioni di uscita avvenivano in modo inverso, con la differenza che la maggior parte dei pallet si dirigevano alle zone di picking.
Fase 3: eliminare il trasporto interno di pallet completi
La crescita dell'azienda non ha comportato un maggior numero di ubicazioni, bensì l’incremento della movimentazione dei pallet. A tale scopo, si è valutata la possibilità di aumentare il numero di carrelli e di operatori, con il conseguente rischio che ciò poteva implicare.
L'impianto aveva quindici corsie di stoccaggio ed erano già presenti cinque carrelli trilaterali. Benché sarebbe stato possibile introdurne altri cinque, si decise di non farlo poiché, poiché trattandosi di mezzi semiautomatici e poco veloci, il numero dei cicli offerti era insufficiente per soddisfare le esigenze di Disalfarm.
Mecalux ha quindi preso in considerazione due possibili opzioni relative all'uso di trasportatori automatici a rulli e a catene per eliminare tutte le movimentazioni dei carrelli frontali o controbilanciati nel magazzino.
Prima opzione fase 3: scartata
La proposta prevedeva una testata composta dai seguenti elementi:
- Due vie principali perpendicolari alle scaffalature.
- Due pettini (uno di entrata e l'altro di uscita) in ciascuna delle corsie di stoccaggio.
- Postazione di entrata e controllo dei pallet nella zona delle baie con rispegimento dei pallet non adatti.
- Uscita diretta alle spedizioni.
- Due uscite alle zone di picking.
Era l'opzione più coerente dal punto di vista della vicinanza alle baie ed era anche valida per alimentare le postazioni di picking.
Per le operazioni di stoccaggio si sarebbero utilizzati i carrelli trilaterali e, in futuro, sarebbe stato proposto di aumentare il numero di carrelli o cercare una soluzione automatica.Inoltre, la parte posteriore sarebbe stata destinata alla zona di cambio corsia per i carrelli trilaterali, come era stato previsto nella prima fase.
Anche se questa soluzione sarebbe stata la più semplice e la più logica, se tutto fosse stato fatto fin dall’inizio sotto queste premesse, venne scartata in quanto per poter essere adottata sarebbe stato necessario arrestare l’intero ciclo operativo del magazzino.
Seconda opzione fase 3: la soluzione
La decisione fu quella di posizionare la parte principale della testata nel lato posteriore del magazzino. In questo modo, come già detto, si lasciava la corsia principale per le manovre di cambio direzione dei trilaterali e per la circolazione dei carrelli frontali.
Questa soluzione era più complessa e costosa, poiché comportava l'installazione di un circuito di rulliere nella parte inferiore di una delle scaffalature per trasferire tutta la merce proveniente dalle baie. Lo stesso accadeva con le uscite, tuttavia era l'unica soluzione realizzabile senza interferire con le operazioni quotidiane.
Le movimentazioni tra i pettini di entrata e le ubicazioni erano effettuate con carrelli trilaterali. Al termine della ricostruzione, la corsia principale era abilitata solo per il cambio di corsia dei carrelli trilaterali e per le poche uscite dirette verso le spedizioni.
Da quel momento, è stato incluso il programma di controllo Galileo di Mecalux, responsabile della gestione di tutte le movimentazioni automatiche delle rulliere, dalla postazione delle entrate alle uscite, passando per la zona di picking. I terminali in radiofrequenza erano ancora utilizzati per dare istruzioni agli operatori dei carrelli trilaterali.
Fase 4: automazione totale del magazzino
Il successo ottenuto con l'automazione delle movimentazioni di entrata e uscita ha fatto sì che, a seguito delle nuove previsioni di crescita, si valutasse la possibilità di automatizzare tutto il magazzino.
La totale automazione comportava un nuovo inconveniente: le macchine automatiche (trasloelevatori) esistenti sul mercato non consentivano di lasciare i pallet a terra. Per rimediare, l'unica opzione plausibile era che il primo livello avesse un'elevazione tra 60 e 70 cm da terra e che si collocasse una guida nella parte superiore delle corsie. Questa soluzione comportava la perdita di un livello del magazzino o, in altri termini,1.290 posti pallet in meno.
Poiché le esigenze di Disalfarm non consentivano la perdita di capacità di stoccaggio, si doveva trovare un'altra via di automazione o costruire un altro centro logistico.
Mecalux lanciò allora sul mercato il trasloelevatore trilaterale, sostituto naturale dei carrelli trilaterali, che si adattava perfettamente alle caratteristiche che richiedeva il centro logistico di Disalfarm.
Le sue caratteristiche sono le seguenti:
- È possibile lasciare i pallet a soli 10 cm da terra.
- Dispone di forche trilaterali invece delle classiche telescopiche laterali.
- Non richiede una guida nella parte superiore delle corsie, solo due guide a terra.
- La sua altezza massima è di 15 m.
- Può disporre di carro di trasbordo (cambio corsia).
- Utilizza Galileo come programma di controllo.
- Offre almeno la stessa capacità dei trilaterali.
Cambiamenti effettuati nella fase 4
I cambiamenti applicati, minimi e facilmente eseguibili, sono stati principalmente:
- Installare le due guide a terra.
- Modificare leggermente le altezze tra i livelli.
- Allungare la postazione di controllo installata sulle rulliere della testata.
- Predisporre delle reti di sicurezza per adeguare l'impianto alle norme in materia di automazione dei magazzini, in particolare quelle relative alla sicurezza nelle corsie in cui operano i trasloelevatori.
Gli accessi alle corsie per le operazioni di manutenzione del magazzino avvengono dal lato contrario alla testata, ossia dove vi era la corsia principale dell'impianto quando funzionava con i carrelli trilaterali.
Per le poche operazioni di uscita dei pallet completi, è stato predisposto un tunnel a gravità per corsia sulle mensole presenti nella testata precedente, alla quale si può accedere con carrelli controbilanciati senza dovere entrare nelle zone di movimentazioni automatiche.
Comunicazione con il software
Fin dall'inizio, Disalfarm disponeva di un sistema di gestione del magazzino (SGM) potente e adattato alle proprie esigenze operative. Continuare a utilizzare questo sistema come base di gestione di tutto il magazzino era una condizione obbligatoria. Per questo, è bastato ricorrere al programma di controllo standard di Mecalux, Galileo Control System, per eseguire tutte le movimentazioni del magazzino.
Inoltre è stata sviluppata un'interfaccia in modo che i sistemi comunichino correttamente, oltre a uno strato intermedio di gestione, per evitare ordini incongruenti riguardo a scorte e occupazione delle ubicazioni.
Vantaggi per Disalfarm
- Elevata capacità di stoccaggio in uno spazio ridotto: il magazzino di Disalfarm consente di stoccare 19.350 pallet da 800 x 1.200 mm.
- Migliorare senza ridurre il servizio: Mecalux ha ottimizzato il centro logistico di Disalfarm senza che l'azienda abbia mai smesso di restare operativa e rimanendo negli stessi impianti.
- Elevata produttività: l'automazione dei diversi processi di stoccaggio ha incrementato il flusso di movimentazioni, adeguandosi alle esigenze della società.
- Controllo totale: l'interfaccia di comunicazione tra il sistema di gestione del magazzino di Disalfarm e il programma di controllo standard di Mecalux consente di gestire tutti i processi e i cicli operativi del magazzino.
Magazzino di Disalfarm | |
---|---|
Capacità di stoccaggio: | 19.350 posti pallet |
Misure del pallet: | 800 x 1.200 mm |
Peso massimo del pallet: | 800 kg |
Altezza delle scaffalature: | 13 m |
Lunghezza delle scaffalature: | 60 m |
N. di trasloelevatori: | 15 |
Tipo di trasloelevatore: | trilaterale automatico |
Galleria
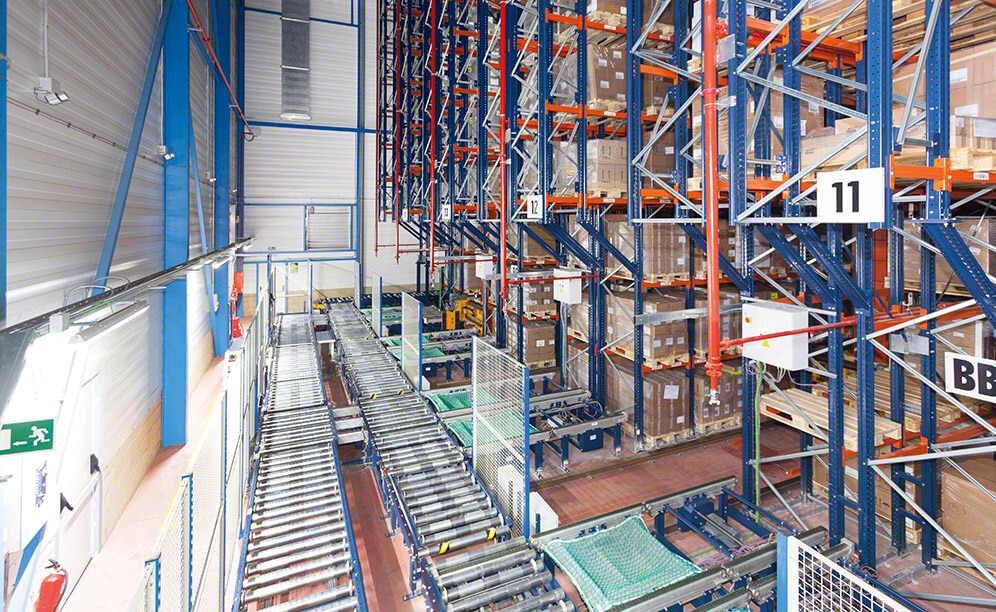
Consultate un esperto