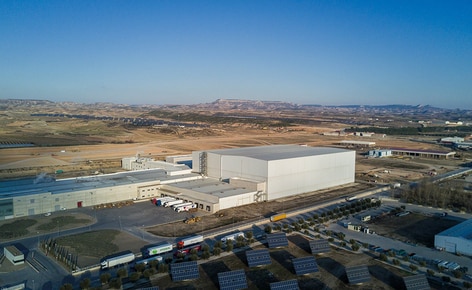
Mecalux accompagna Congelados de Navarra nella sua crescita costante
Capacità pari a 146.000 posti pallet su tre celle di surgelazione automatiche per Congelados de Navarra
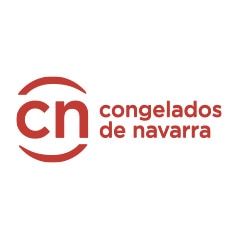
Fondata nel 1998, Congelados de Navarra è la società di alimenti surgelati più giovane d'Europa e con un percorso ancora più solido. La sua chiara vocazione per la tecnologia e l'innovazione in tutti i processi produttivi l'ha portata a posizionarsi tra le prime dieci aziende specializzate in verdure surgelate del continente. Fin dall'inizio, Mecalux ha accompagnato questa azienda nei suoi obiettivi di espansione, progettando e implementando le soluzioni logistiche più efficienti per soddisfare le sue esigenze.
Una storia di successo
Congelados de Navarra è un esempio di impegno e successo, uniti a un grande spirito imprenditoriale. La sua storia inizia nel 1998, quando Benito Jiménez fondò l'azienda e avviò la costruzione del centro produttivo nella località di Arguedas (Navarra).
Inizialmente, il centro era formato da una cella di surgelazione con sistema drive-in, ma la sua capacità non era sufficiente per supportare l'incremento delle vendite. La società scelse quindi di fare un investimento strategico di ampliamento, rendendosi fin da subito conto dell'importanza e della necessità di automatizzare il magazzino per aumentare il rendimento e la produttività di tutti i suoi processi.
Attualmente, il centro di Arguedas dispone di due celle di surgelazione completamente automatiche, che offrono una capacità di 12.700 posti pallet. L'azienda ha sempre usufruito dei vantaggi dell'automatizzazione per ottimizzare il rendimento del suo centro.
Sperimenta una crescita continua, raggiungendo obiettivi di prestigio, come quello di maggiore produttore europeo di broccoli surgelati nel 2004. Date le prospettive di crescita, nel 2008 Congelados de Navarra inaugurò il suo secondo centro produttivo, ubicato a Fustiñana (a solo 24 km dalla prima fabbrica). Questo centro si è ampliato e adattato ai requisiti dell'azienda.
Ora, dispone di due celle automatiche autoportanti con una capacità totale di 63.000 posti pallet e sta per costruire una terza cella, che avrà una capacità di 83.000 posti pallet.
Nel 2012, la società ha aperto la sua prima sede in Francia, dando il via all'espansione internazionale.
Oggi possiede filiali anche nel Regno Unito e negli Stati Uniti.Esporta il 70% della sua produzione e ha costituito un'estesa rete di distributori e importatori che la aiutano a commercializzare i suoi prodotti in tutto il mondo.
Mecalux e Congelados de Navarra
La collaborazione tra le due organizzazioni risale al 1998, in concomitanza con gli inizi di Congelados de Navarra.
Con la consulenza di Mecalux, l'azienda si è proposta e ha sviluppato nuovi obiettivi e progetti che hanno migliorato la sua logistica. Queste sono alcune delle strutture realizzate finora:
Arguedas
Nel 2000, Congelados de Navarra ha richiesto a Mecalux la costruzione della cella di surgelazione automatica (in una cella di struttura tradizionale) nel suo centro produttivo ad Arguedas. È stato installato il sistema a stoccaggio intensivo con Pallet Shuttle e trasloelevatore con una capacità di stoccaggio di 3.800 posti pallet.
Nel 2004, è stata avviata la seconda cella automatica e autoportante, di fianco alla prima. Misura 33 m di altezza ed è composta da tre corsie con scaffalature a doppia profondità su entrambi i lati, che offrono una capacità di stoccaggio di 8.900 posti pallet, il triplo della capacità iniziale.
Fustiñana
Nel 2008, Congelados de Navarra ha inaugurato un nuovo centro produttivo a Fustiñana, con l'obiettivo di mantenere il ritmo di crescita previsto e servire velocemente i suoi clienti.
Di fatto, questo ambizioso progetto si è esteso ed è cresciuto in diverse tappe:
- Fase 1
Mecalux ha realizzato una cella automatica autoportante alta 36 m, che funziona a una temperatura costante di -21 ºC. È formata da sei corsie, con scaffalature a doppia profondità, con una capacità di stoccaggio di 27.000 posti pallet.
In questo centro, tutto il trasporto interno tra le diverse aree di produzione e la cella è completamente automatizzato, attraverso un circuito di convogliatori a rulli, navette, elevatori ed elettrovie.
- Fase 2
Tra il 2010 e il 2011 è stata costruita una nuova cella dalle caratteristiche simili alla precedente, adiacente e integrata alla prima, con una capacità di altri 36.000 posti pallet, distribuiti in otto corsie.
- Fase 3
Nel 2015, Congelados de Navarra ha ampliato l'area di confezionamento e miscelatura. Si è affidata nuovamente a Mecalux per installare tutti i mezzi di movimentazione interna che collegano queste zone con il resto delle aree di produzione, compresi i magazzini.
- Fase 4
Un anno dopo, Congelados de Navarra ha richiesto la collaborazione di Mecalux per trovare una soluzione per affrontare comodamente gli eventuali incrementi di produzione e rafforzare così la sua crescita, sia in termini di produttività che di capacità di stoccaggio.
Si è deciso di costruire un'altra cella, complementare alle due precedenti e completamente destinata ai prodotti semilavorati. Quando verrà conclusa, sarà collegata ai circuiti di trasporto interni già esistenti, per trasferire la merce in entrambe le direzioni.
Il magazzino misurerà 43 m di altezza con una capacità di 83.000 posti pallet, una costruzione di proporzioni colossali, inusuale in questo tipo di celle. È attrezzato con il sistema automatico a stoccaggio intensivo Pallet Shuttle con navette, che consente di raggiungere un numero molto elevato di movimentazioni.
Efficiente installazione a Fustiñana
Nel centro di Fustiñana si fabbrica la maggior parte della produzione di Congelados de Navarra. Gli alimenti devono superare una serie di processi (la maggior parte di essi automatici) per garantire la massima qualità e mantenere la giusta consistenza, i valori nutrizionali e sapori ottimali.
Uscita dalla produzione
L'impianto di Mecalux inizia quando la merce ha attraversato il tunnel di surgelazione. Sono state montate delle rulliere sotto le linee di smistamento. Gli octabin vuoti (grandi confezioni di cartone e plastica che contengono prodotti sfusi) vengono spostati fino alle tramogge e riempiti con i prodotti.
Successivamente, una navetta trasferisce i pallet fino agli elevatori, che li portano al livello superiore, luogo in cui le fasciatrici automatiche chiudono gli octabin e mettono in sicurezza il prodotto.
Una volta verificato il loro stato, entrano nel circuito di elettrovie, dirigendosi alle celle di stoccaggio (o alle restanti aree di produzione).
La progettazione del circuito di elettrovie consente di disporre delle navette necessarie in ogni punto per assegnazione a gravità. Inoltre, sono previste scorciatoie per evitare che le navette debbano realizzare il percorso completo.
Entrata nelle celle
Prima di introdurli nel magazzino, i pallet attraversano un SAS (Security Airlock System). Si tratta di una precella composta da due porte veloci (una di esse dà sulla cella e l'altra sull'esterno) che non sono mai aperte contemporaneamente.
Questo sistema viene utilizzato per evitare cambiamenti bruschi di temperatura, perdita di freddo e condensazioni. È stato installato anche un SAS per l'uscita dei pallet che si dirigono verso le aree di elaborazione.
Le celle dispongono di due livelli di comunicazione e in entrambe vi sono due circuiti di rulliere, uno per le entrate e un altro per le uscite.
Nel livello superiore avviene l'entrata della merce proveniente dalla produzione e l'uscita dei pallet che si avviano verso le aree di elaborazione (confezionamento e miscelatura).
Nel livello inferiore vi è l'entrata dei prodotti dall'esterno del magazzino ed è stata anche ubicata l'area di spedizione.
Caratteristiche delle celle
Le due celle unite hanno le seguenti dimensioni:140 m di lunghezza, 103 m di larghezza e 35 m di altezza.
Sono composte da un totale di 14 corsie con scaffalature a doppia profondità su ogni lato, raggiungendo una capacità di stoccaggio totale di 63.000 posti pallet.
Si tratta di una costruzione autoportante, ossia le scaffalature sostengono il proprio peso, quello della pannellatura e della copertura, oltre a quello della merce. Nella parte superiore delle scaffalature vi sono le tralicciature nelle quali sono situati i dispositivi di raffreddamento. In questo modo, si ottiene un flusso d’aria continuo e una diffusione uniforme della temperatura in tutto l'impianto.
In ogni corsia, i trasloelevatori bicolonna trasferiscono i pallet dalle rulliere di entrata e uscita alle ubicazioni delle scaffalature assegnate dal software di gestione magazzini (SGM) Easy WMS di Mecalux, in base alle impostazioni precedentemente configurate.
Sono state adibite passerelle e piattaforme nella parte superiore delle celle per poter eseguire gli interventi di manutenzione dei dispositivi di raffreddamento e dei trasloelevatori. Vi si accede dalla parte esterna del magazzino.
Livello inferiore delle celle
L'uscita dei prodotti verso le spedizioni avviene nel livello inferiore delle celle. Un circuito di rulliere unisce le corsie di stoccaggio con le porte di uscita che danno sulle precelle, dove si depositano i pallet in attesa, fino al momento di essere distribuiti nei veicoli di trasporto.
Nella precella (con altezza ridotta e temperatura controllata) si raggruppa la merce di uno stesso ordine o percorso, per velocizzare il successivo carico sui camion di distribuzione. In questo spazio possono essere contenuti 500 pallet pronti per la spedizione.
Sono presenti tre SAS che collegano la precella con la zona delle baie. Una volta attraversate, i pallet sono a disposizione degli operatori, per poter essere caricati sugli automezzi.
In questa stessa zona si trovano le postazioni di entrata per i prodotti proveniente dall'esterno dell'impianto di produzione. I pallet che non rispettano determinati parametri qualitativi vengono posti su un pallet schiavo, che può essere di due misure diverse: 800 x 1.200 mm o 1.000 x 1.200 mm.
Area di confezionamento e miscelatura
I prodotti diretti all'area di elaborazione abbandonano le celle dal livello superiore e vengono ritirati dalle elettrovie.
L'area di elaborazione è più elevata rispetto al circuito di trasporto delle elettrovie. Per questo motivo, sono stati installati elevatori che portano la merce al livello superiore. Lì si trovano le tramogge di confezionamento e miscelatura, oltre a un circuito di rulliere che consegna i pallet nella relativa postazione.
I pallet che sono stati respinti a seguito di questi processi vengono portati giù tramite gli elevatori e sono trasferiti dalle elettrovie verso la nuova destinazione.
Invio di octabin alla produzione
L'invio di octabin vuoti alla produzione è fondamentale per il corretto funzionamento di questo centro; anche in questo caso, si tratta di un'operazione che viene eseguita automaticamente.
Gli octabin vengono ricondizionati in una zona specifica: si collocano su pallet, vengono rivestiti con un sacco di grandi dimensioni che evita il contatto tra il prodotto surgelato e il cartone e, infine, sono identificati con un codice RFID.
Due elevatori inviano gli octabin al livello di trasporto e le elettrovie li trasferiscono automaticamente ai relativi punti.
Elettrovie
Le elettrovie sono il punto di unione di questo impianto e si occupano del movimento interno tra tutte le aree del centro produttivo.
I binari sono appesi al soffitto e da lì le navette prendono la corrente e rilevano la loro posizione nel circuito. Le deviazioni sono fondamentali; vi sono scorciatoie, zone di manutenzione e navette in attesa.
Le elettrovie sono molto agili e garantiscono un flusso costante di merce. Sono ideali in aziende di alimentazione come Congelados de Navarra, poiché non creano ostacoli a terra, agevolando le operazioni di pulizia.
Easy WMS di Mecalux, il cervello di tutto il sistema
Gestione logistica ottimale
Il software sviluppato da Mecalux gestisce e interviene in tutti i processi eseguiti in un impianto, tra cui l'entrata della merce proveniente dalla produzione e dall'esterno, l'assegnazione di ubicazioni, il controllo dello stock, lo stoccaggio, il prelievo, l'invio di pallet alle aree di elaborazione, i resi al magazzino e così via.
Easy WMS di Mecalux fornisce ininterrottamente octabin vuoti per il continuo riapprovvigionamento delle uscite dalla produzione.
Quando viene stoccata la merce nelle relative ubicazioni, si seguono le regole e gli algoritmi che tengono conto delle caratteristiche dei prodotti, dei criteri di consumo e della loro rotazione. Le regole sono configurate in Easy WMS di Mecalux per smistare lo stock tra le 14 corsie delle celle. In questo modo, il prodotto sfuso in octabin viene depositato il più vicino possibile alla zona di confezionamento e miscelatura. Il prodotto elaborato, invece, viene ubicato vicino alla zona di spedizioni.
L'applicazione ERP dell'azienda, JD Edwards di Oracle, richiama i prodotti sfusi per la zona di confezionamento. L'SGM di Mecalux calcola la quantità di octabin necessari e li invia verso la loro destinazione seguendo una sequenza predefinita. Gli ordini che vengono trasferiti verso la zona di miscelatura ricevono lo stesso trattamento da parte dell'SGM di quelli per il confezionamento.
Le spedizioni vengono effettuate per mezzo di camion. L'SGM genera operazioni di prelievo degli ordini dalle loro ubicazioni e li deposita nelle precelle, in attesa di essere trasferiti alle baie. Quando il camion si avvicina alla baia per essere caricato, i pallet partono automaticamente verso la postazione di uscita e una schermata di Easy WMS indica all'operatore verso quale baia deve essere diretto ogni carico.
Triangolo di comunicazione
Per il corretto funzionamento del magazzino, Easy WMS di Mecalux è in comunicazione permanente con gli altri due sistemi di gestione utilizzati in questo progetto: il sistema di gestione aziendale ERP di Congelados de Navarra e il sistema di controllo della produzione (MES).
Il sistema MES indica a Easy WMS le entrate di prodotti che si stanno effettuando in tempo reale per ogni linea di produzione. Consente inoltre di effettuare l'invio dei prodotti sfusi a questa zona.
L'applicazione ERP notifica l'entrata dei pallet provenienti da altri centri logistici di Congelados de Navarra, diretti alla zona di stoccaggio, e permette inoltre di effettuare ordini di prodotti sfusi per il confezionamento o la miscelatura.
Galileo, il cuore dell'impianto
Un magazzino automatico della complessità di Congelados de Navarra richiede soluzioni che permettano di semplificarne e ottimizzarne la gestione. In questo senso, il software di controllo Galileo di Mecalux funziona come coordinatore generale dell'impianto, eseguendo le movimentazioni dei dispositivi elettromeccanici che svolgono le operazioni di trasporto e stoccaggio della merce.
Galileo si occupa della movimentazione delle macchine (rulliere, trasloelevatori, elettrovie, elevatori, ecc.), controlla i componenti hardware (scanner, lettori RFID, variatori, ecc.) e registra i possibili problemi o guasti, oltre a tutte le comunicazioni con il software di gestione magazzini (SGM). In poche parole, riceve gli ordini dall'SGM, invia i relativi segnali alla macchina e controlla lo spostamento automatico degli octabin.
Inoltre, l'utilizzo del sistema SCADA fornisce tutte le informazioni in tempo reale su ogni singola macchina, sui guasti, sui trasporti in movimento ecc., del magazzino senza necessità di utilizzare hardware di visualizzazione specifico.
A prova di futuro
Il centro produttivo a Fustiñana è predisposto per la crescita e contempla la possibilità di costruire più celle in futuro, in base alle esigenze di mercato e agli obiettivi dell'azienda.
Il software offerto da Mecalux accompagnerà sempre l'azienda, adeguandosi ai cambiamenti e all'aumento della produzione. È un sistema scalabile, ossia in grado di incrementare o ridurre le risorse e la potenza in base ai requisiti del centro.
A tale scopo, per garantire il buon funzionamento della nuova cella di congelamento, Easy WMS disporrà di un modulo per l'uso del sistema Pallet Shuttle automatico con navette.
Prospettive future
Benito Jiménez, imprenditore e fondatore di Congelados de Navarra, ha deciso di adottare sistemi automatici in tutti i processi, dalla produzione fino allo stoccaggio, compreso il trasporto interno.
Lo scopo è aumentare il rendimento dei suoi centri e rafforzare il ritmo di crescita dell'azienda.
L'automazione di tutte le aree di stoccaggio dei centri di Arguedas e Fustiñana rappresenta un reale vantaggio competitivo per Congelados de Navarra, ottimizzando la capacità di stoccaggio con il minimo intervento umano.
Da sempre, Mecalux ha fornito consulenza a Congelados de Navarra per realizzare i suoi progetti di espansione. Ha fornito tutto il suo solido know-how e la sua vasta esperienza per trovare soluzioni personalizzate e che possano risolvere efficientemente le esigenze logistiche proposte. Frutto di questa solida partnership, il centro automatico di Fustiñana è uno dei più moderni e tecnologicamente sviluppati del mercato europeo, oltre a essere un riferimento a livello mondiale.
Galleria
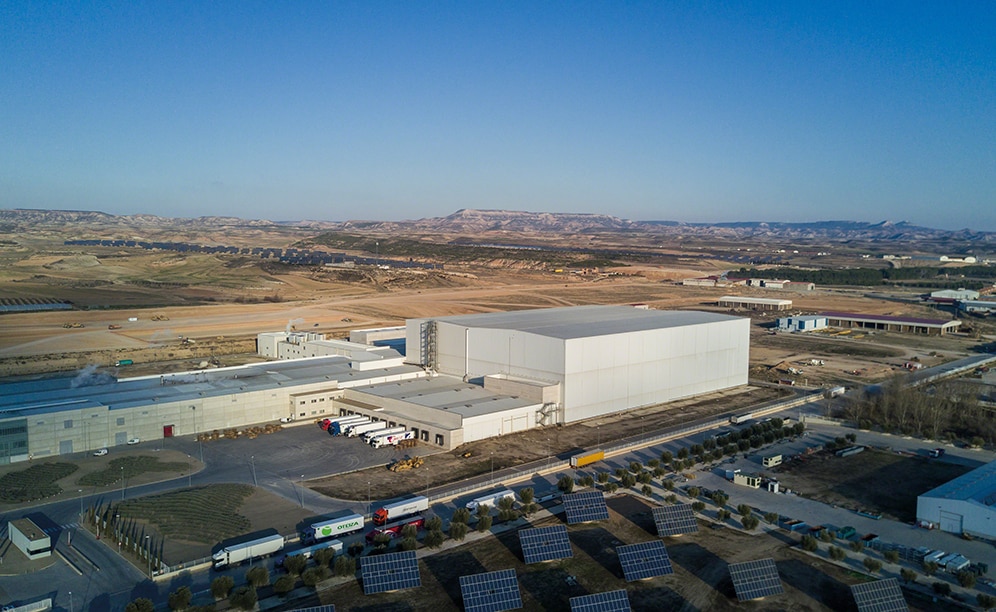
Consultate un esperto